Mass customization is revolutionizing the way products are made, and 3D printing is at the forefront of this movement. By combining the concepts of customization and manufacturing, mass customization allows consumers to have personalized products that are tailored to their individual preferences. This article will explore the concept of mass customization, the role of 3D printing in facilitating it, and provide case studies, benefits, and challenges associated with 3D printing in mass customization.
Understanding Mass Customization
Mass customization is the process of combining the efficiency and cost benefits of mass production with the personalization and customization of individual products. It aims to provide consumers with the ability to have unique products that meet their specific needs, while still maintaining economies of scale. This approach deviates from the traditional mass production model, which focuses on producing large quantities of identical products.
Mass customization has revolutionized the way consumers interact with products. In the past, consumers had limited options when it came to purchasing goods. They were forced to choose from a limited selection of standardized products that may not have fully met their needs or preferences. However, with the advent of mass customization, consumers now have the power to design and personalize products to their exact specifications.
The concept of mass customization is not a new one. In fact, it has been around for centuries, although not in the same form as we know it today. Artisans and craftsmen would often tailor their products to suit the individual needs and preferences of their customers. This personalized approach to production ensured that each customer received a unique product that was tailored to their specific requirements.
The Evolution of Mass Customization
Mass customization has evolved over the years due to advancements in technology and changing consumer demands. In the past, customization was a costly and time-consuming process limited to luxury products. However, with the introduction of digital technologies and automated manufacturing processes, mass customization has become more accessible and affordable for a wider range of products.
Advancements in computer-aided design (CAD) software and 3D printing technology have played a significant role in the evolution of mass customization. These technologies have made it easier for manufacturers to create and produce customized products on a large scale. With CAD software, designers can easily create digital models of products and make modifications to suit individual customer preferences. These digital models can then be used to guide the manufacturing process, ensuring that each product is customized to the customer's specifications.
Another key factor in the evolution of mass customization is the rise of e-commerce. Online platforms have made it easier for consumers to access and customize products from the comfort of their own homes. Consumers can now browse through a wide range of options, select the features and specifications they desire, and place an order for a customized product with just a few clicks.
Furthermore, advancements in supply chain management and logistics have also contributed to the growth of mass customization. Manufacturers are now able to efficiently manage the production and delivery of customized products, ensuring that they reach the customer in a timely manner. This streamlined process has made mass customization a viable option for businesses of all sizes.
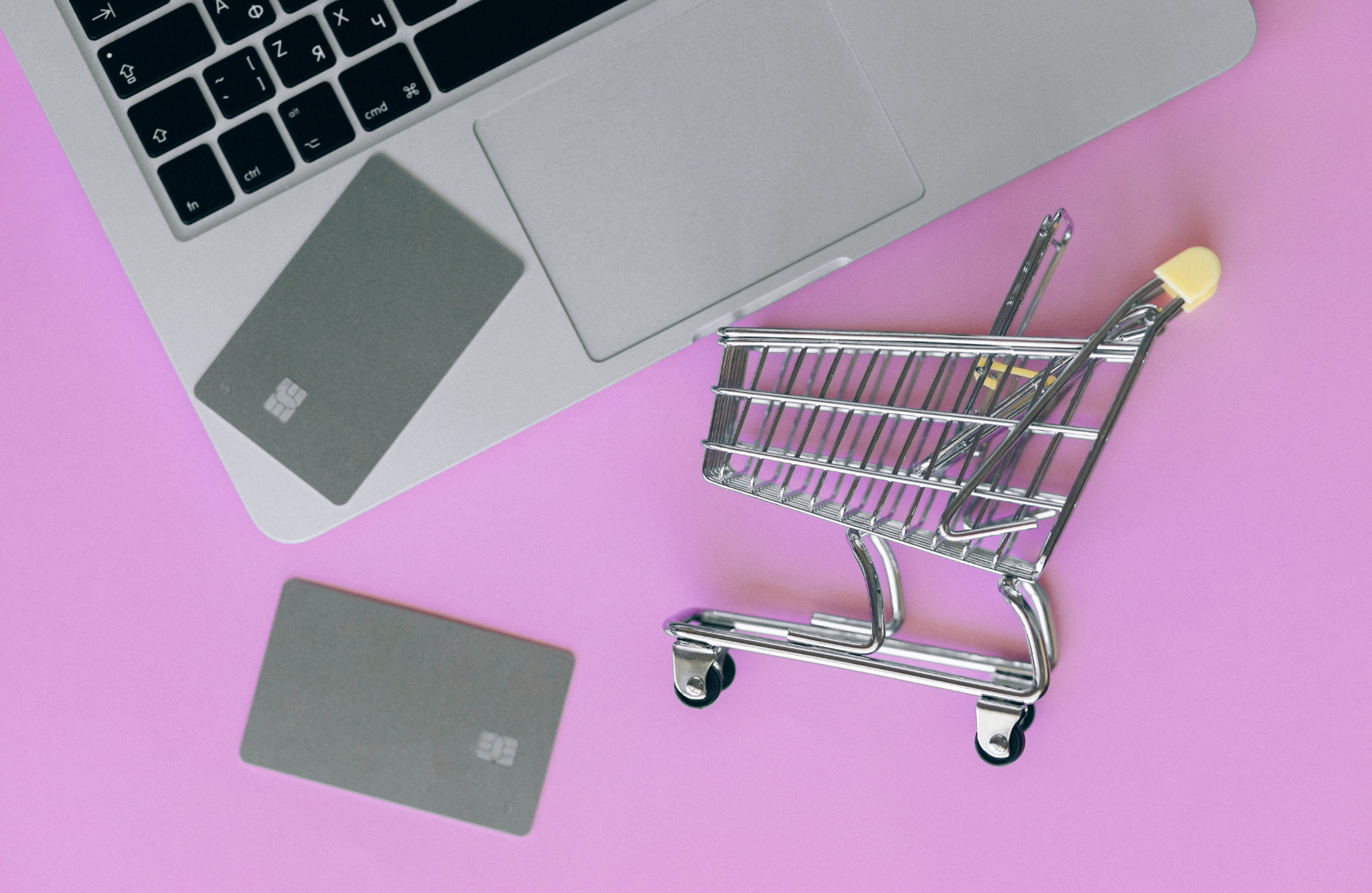
The Role of 3D Printing in Mass Customization
An Introduction to 3D Printing
3D printing, also known as additive manufacturing, is a process of creating three-dimensional objects by adding layers of material. It works by converting digital designs into physical objects, making it ideal for producing customized products. Unlike traditional manufacturing processes that involve subtracting material through milling or molding, 3D printing builds objects layer by layer, allowing for greater design freedom and customization.
When it comes to 3D printing, the possibilities are endless. From intricate jewelry designs to complex architectural models, this technology has revolutionized the way products are made. By harnessing the power of computer-aided design (CAD) software, designers can create intricate and detailed objects that were once thought to be impossible to manufacture.
One of the key advantages of 3D printing is its ability to produce highly customized products. Traditional manufacturing methods often involve producing large quantities of identical items, which limits the ability to cater to individual customer preferences. With 3D printing, products can be easily customized by modifying the digital design file. This flexibility allows manufacturers to produce personalized products without incurring significant additional costs or production time.
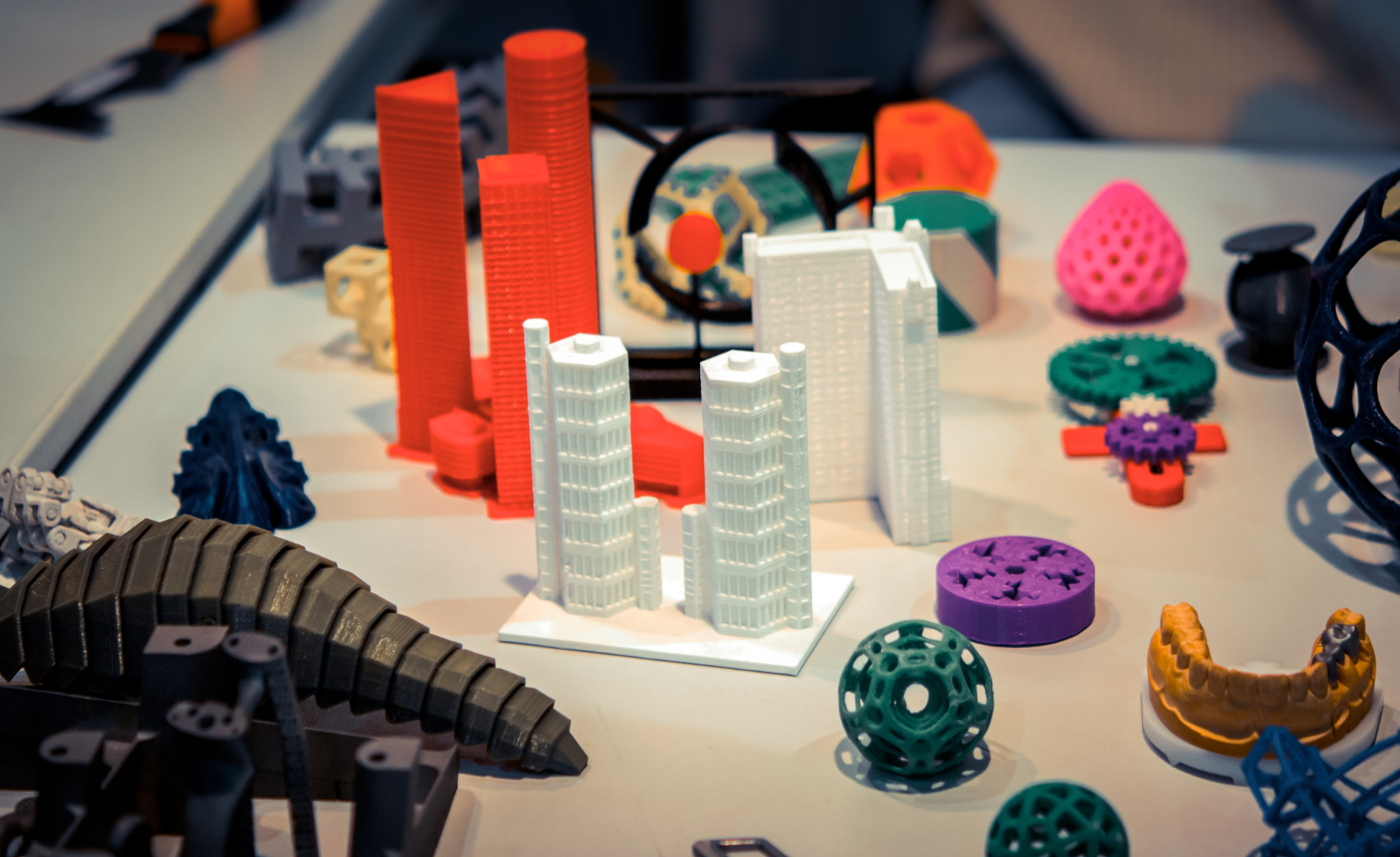
How 3D Printing Facilitates Mass Customization
3D printing plays a pivotal role in enabling mass customization by eliminating many of the barriers that traditional manufacturing faces. With the ability to create unique products at scale, businesses can now cater to the individual needs and preferences of their customers.
Moreover, traditional manufacturing processes often require the creation of specialized molds or tooling, which can be expensive and time-consuming. In contrast, 3D printing eliminates the need for molds, as products are built layer by layer directly from the digital design. This not only reduces upfront costs but also enables manufacturers to quickly iterate and modify designs as needed.
Imagine a world where every consumer can have a product tailored specifically to their needs and desires. With 3D printing, this vision becomes a reality. From customized orthopedic implants that perfectly fit an individual's body to personalized fashion accessories that reflect one's unique style, the possibilities are truly limitless.
Furthermore, 3D printing has the potential to revolutionize the healthcare industry. With the ability to create patient-specific medical devices and prosthetics, medical professionals can provide better care and improved outcomes for their patients. This technology allows for the production of customized hearing aids, dental implants, and even artificial limbs that are tailored to the individual's anatomy.
3D printing also has significant implications for the automotive industry. With the ability to produce lightweight and complex parts, manufacturers can create vehicles that are not only more fuel-efficient but also safer. Customized car parts can be designed to fit specific models or even individual drivers, enhancing both performance and comfort.
Another area where 3D printing is making a significant impact is in the field of architecture. Architects and designers can now create intricate scale models of their buildings, allowing for a better understanding of the design and its impact on the surrounding environment. This technology also enables the production of custom-made building components, reducing construction waste and improving efficiency.
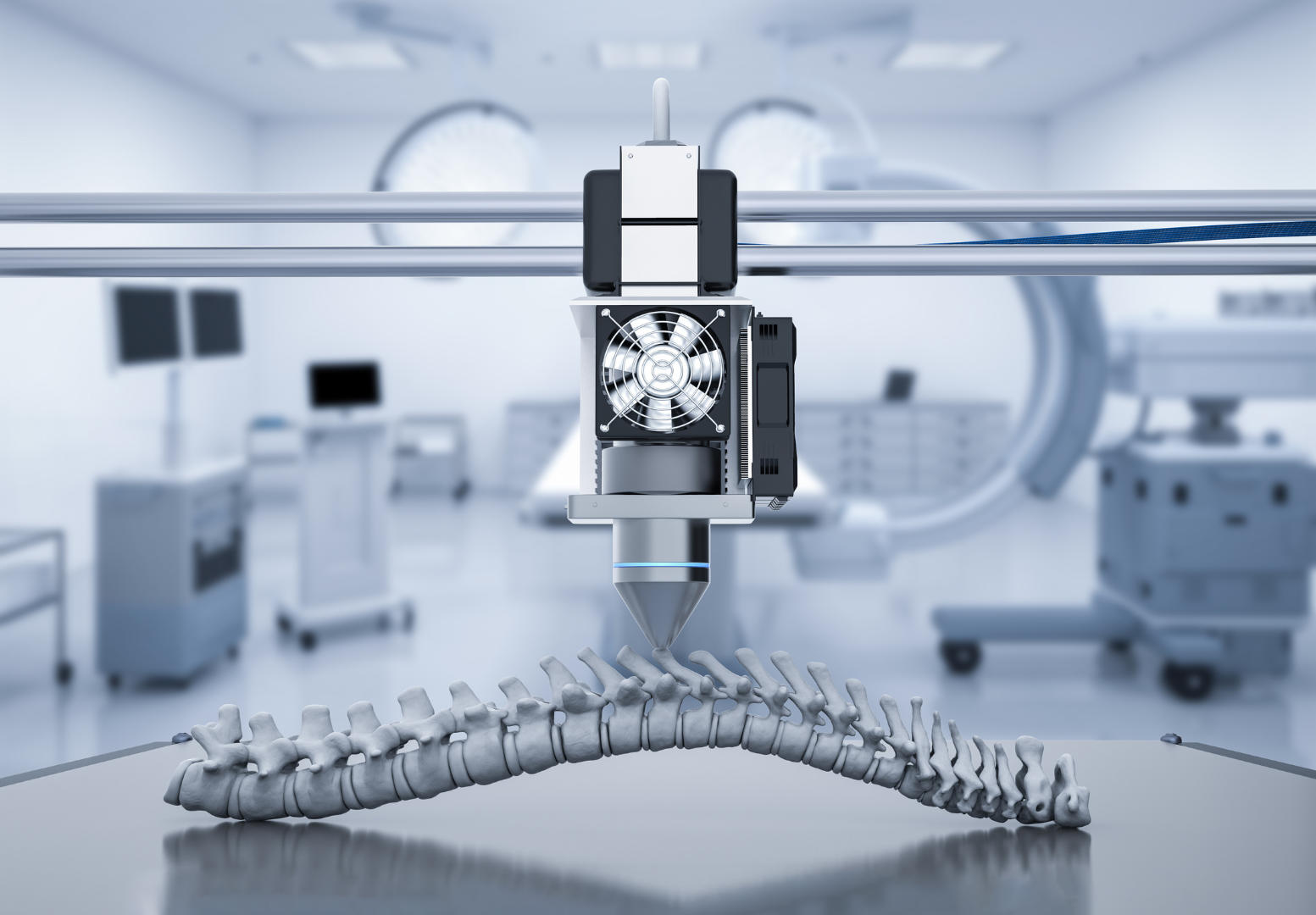
Case Studies of 3D Printing in Mass Customization
3D Printing in the Fashion Industry
The fashion industry is embracing 3D printing as a tool for mass customization. Designers can create unique and customized garments that perfectly fit individual customers. By scanning customers' body measurements and using 3D printing technology, fashion brands can produce garments that are tailored for each person, enhancing fit and comfort. Additionally, 3D printing allows for intricate and complex designs that would be challenging to create using traditional manufacturing methods.
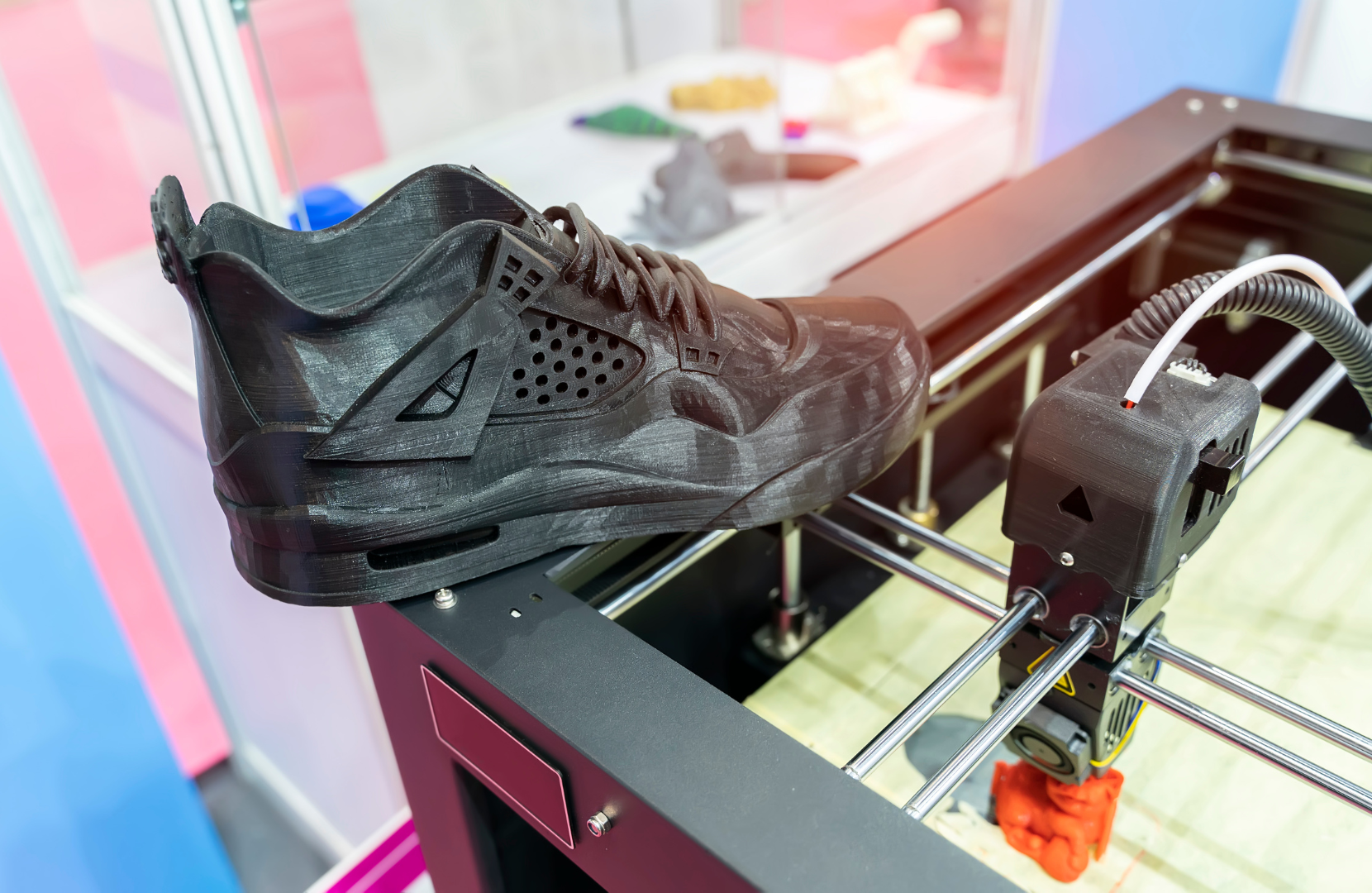
Personalized Products in the Medical Field
The medical field is another sector benefiting from the use of 3D printing in mass customization. Prosthetics, orthotics, and medical implants can be customized to fit the specific needs of patients. By using 3D scanning and modeling, medical professionals can create personalized solutions that improve patient outcomes. Furthermore, 3D printing enables the production of complex anatomical models, aiding in surgical planning and training.
The Benefits of 3D Printing in Mass Customization
Enhancing Product Variety
3D printing allows for endless design possibilities, enabling a wide range of product variations and customization options. This enhances consumer choice and satisfaction, as they can have products that reflect their individual tastes and preferences. The ability to offer a diverse range of customized products sets businesses apart from their competitors, leading to increased customer loyalty and market differentiation.
Reducing Production Time and Costs
Traditional manufacturing often involves long lead times and high production costs, especially for small-batch or customized products. 3D printing streamlines the production process by eliminating the need for tooling, reducing setup times, and enabling on-demand manufacturing. This results in shorter lead times and lower costs, making mass customization economically viable for businesses.
Challenges and Solutions in 3D Printing for Mass Customization
Addressing Quality Control Issues
As with any manufacturing process, ensuring product quality and consistency is crucial. 3D printing faces challenges related to material properties, layer adhesion, and surface finishes. However, advancements in materials and printing techniques are continuously improving the overall quality of 3D-printed products. Additionally, rigorous quality control measures, such as post-processing and testing, can be implemented to address these challenges and ensure that customized products meet the desired standards.
Overcoming Design and Production Challenges
Designing products for 3D printing requires a different approach compared to traditional manufacturing. Designers must consider factors such as structural integrity, material compatibility, and printability. Overcoming these design challenges often involves collaboration between designers and engineers to optimize designs for 3D printing. Moreover, scaling up production while maintaining customization can pose production challenges, but implementing efficient workflows and leveraging automation can help address these issues.
Mass customization, powered by 3D printing, is transforming the way products are made. The ability to personalize products to meet individual needs offers numerous benefits to consumers and businesses alike. With its flexibility, cost-effectiveness, and design freedom, 3D printing is paving the way for a future where customization is the norm, allowing products to truly be tailored to each person's preferences. As technology continues to advance, the possibilities for mass customization through 3D printing will only continue to grow.