Stereolithography, also known as SLA, is a revolutionary technology that lies at the core of 3D printing. This article aims to provide a comprehensive understanding of stereolithography, exploring its basic concept, history, role in 3D printing, the process itself, applications, and future trends.
What is Stereolithography?
Stereolithography is an additive manufacturing process that uses a photopolymerization technique to create three-dimensional objects layer by layer. It was first introduced in the 1980s by Charles W. Hull, the co-founder of 3D Systems Corporation. Stereolithography allows the creation of complex shapes that would be otherwise challenging or impossible to produce with traditional manufacturing methods.
Stereolithography revolutionized the manufacturing industry by introducing a new way to fabricate objects. The process combines the precision of computer-aided design (CAD) software with the versatility of photopolymerization, resulting in the production of highly detailed and intricate structures.
One of the key advantages of stereolithography is its ability to create objects with exceptional surface finish and fine details. The layer-by-layer approach ensures that even the most intricate features are accurately reproduced, making it ideal for applications that require high precision, such as jewelry making, dental prosthetics, and medical device manufacturing.
The Basic Concept of Stereolithography
At its core, stereolithography involves the use of a photosensitive liquid resin that solidifies when exposed to ultraviolet (UV) light. The process begins with the creation of a digital model using computer-aided design (CAD) software. This model is then sliced into thin layers, and each layer is traced onto the surface of the liquid resin using a UV laser. The resin solidifies where it is exposed to the laser, creating a solid layer. The build platform is then lowered, and the process repeats, layer by layer, until the final object is formed.
During the stereolithography process, the liquid resin undergoes a chemical reaction called photopolymerization. When the UV laser hits the resin, it triggers a polymerization reaction, causing the resin molecules to link together and form a solid structure. This solidification process is highly controlled, ensuring that each layer is precisely formed and adheres to the previous layers.
After the object is fully printed, it is typically rinsed with a solvent to remove any uncured resin and then post-cured to strengthen the material and enhance its mechanical properties. The post-curing process involves exposing the printed object to additional UV light, which further solidifies the resin and improves its overall durability.
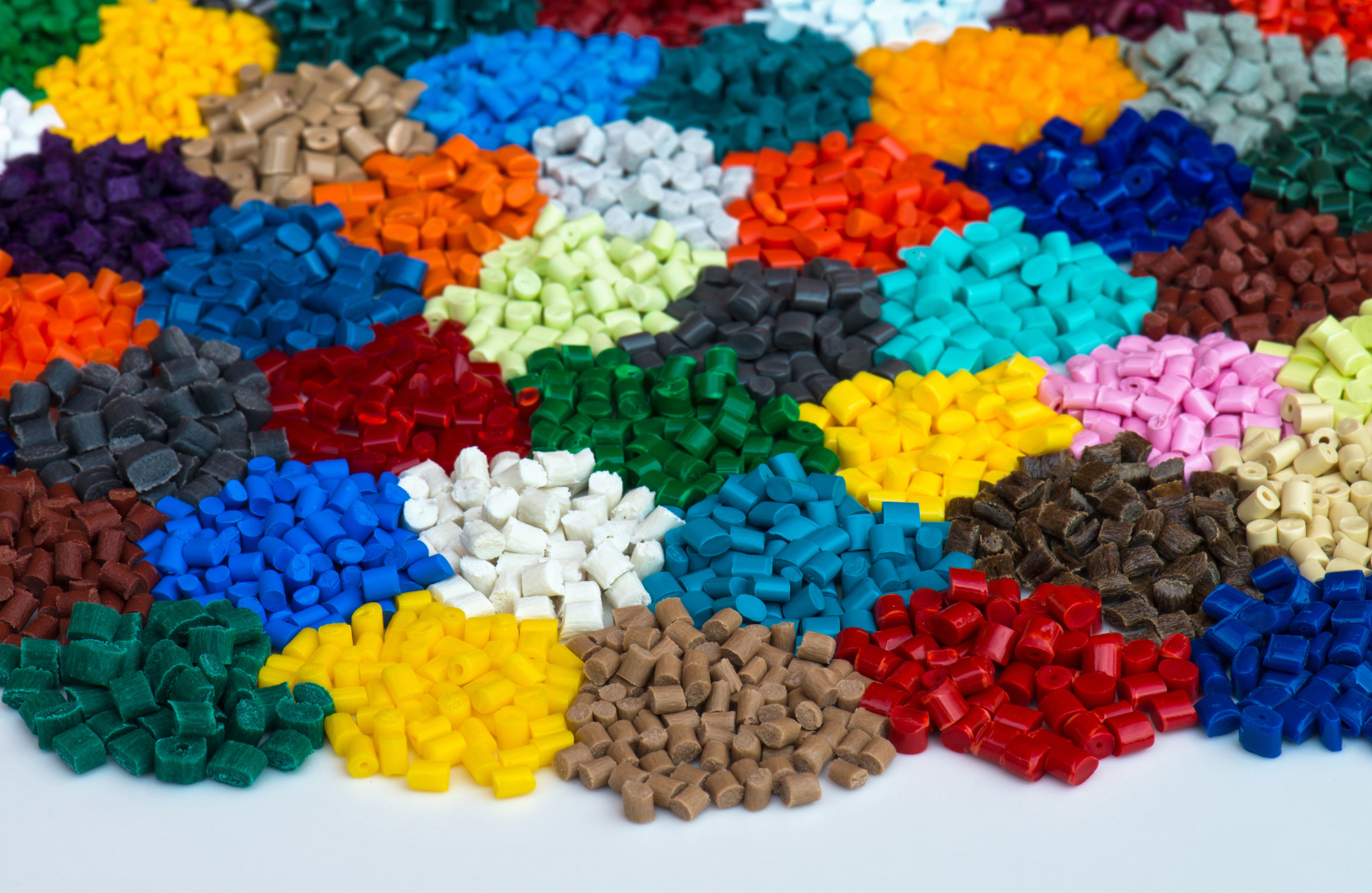
The History and Evolution of Stereolithography
Stereolithography has come a long way since its inception. In the early years, the technology was limited in terms of materials, resolution, and size. However, advancements in materials science, laser technology, and software have greatly expanded the capabilities of stereolithography. Today, a wide range of resins is available, allowing for the production of objects with varying properties, such as flexibility, strength, and transparency.
Furthermore, the introduction of high-resolution projectors and continuous digital light processing (cDLP) has significantly improved the speed and accuracy of the process, making it more accessible and efficient for various applications.
The continuous development and refinement of stereolithography have led to its widespread adoption in various industries. From prototyping and product development to custom manufacturing and art, stereolithography has proven to be a versatile and reliable technology. Its ability to create complex geometries, intricate details, and smooth surfaces has made it a go-to choice for designers, engineers, and artists alike.
As the field of additive manufacturing continues to evolve, stereolithography remains at the forefront, pushing the boundaries of what is possible. With ongoing research and innovation, it is expected that stereolithography will continue to advance, opening up new opportunities and applications in the future.
The Role of Stereolithography in 3D Printing
Stereolithography plays a crucial role in the field of 3D printing. Its ability to produce complex geometries with fine details and high accuracy has made it an essential tool in various industries. From rapid prototyping to custom manufacturing, stereolithography offers numerous advantages over traditional manufacturing methods.
How Stereolithography Works in 3D Printing
When it comes to 3D printing, stereolithography is often the technology of choice for creating concept models, functional prototypes, and even end-use parts. Its layer-by-layer approach allows for the production of intricate designs, eliminating the need for assembly of complex components. With the ability to print in fine resolutions, stereolithography can capture intricate details and produce smooth surfaces, delivering high-quality models and parts.
Advantages of Stereolithography in 3D Printing
One of the key advantages of stereolithography is its versatility in material selection. Resins with various properties, such as transparency, rigidity, or flexibility, can be used to meet specific project requirements. Additionally, stereolithography offers fast turnaround times, enabling rapid iteration of designs and reducing time to market. Its high precision and accuracy also contribute to minimizing material waste and achieving consistent results.
Another significant advantage of stereolithography is its ability to create complex internal structures, such as hollow parts or lattice structures, which can reduce weight without compromising strength. This feature has proven particularly beneficial in industries like aerospace and automotive, where lightweight components can lead to improved fuel efficiency and performance.
.png)
The Process of Stereolithography
The stereolithography process involves several crucial steps and considerations. Understanding each stage is crucial for achieving optimal results and avoiding potential pitfalls.
Step-by-Step Guide to Stereolithography
- Design a 3D model using CAD software.
- Prepare the model for printing, ensuring proper support structures are included.
- Slice the model into thin layers using specialized software.
- Clean the vat and fill it with the desired resin.
- Prep the build platform and calibrate the machine.
- Initiate the printing process, allowing the UV laser to trace each layer and solidify the resin.
- Monitor the process, ensuring proper layer adhesion and overall print quality.
- Once the print is complete, remove the object from the build platform.
- Post-process the object, removing support structures and cleaning the surface.
Materials Used in Stereolithography
One of the key factors that contribute to the success of stereolithography is the selection of appropriate materials. Different resins offer specific mechanical, thermal, and aesthetic properties, enabling a wide range of applications.
Some common materials used in stereolithography include:
- Standard Resins: These resins offer a good balance between strength, detail, and resolution. They are suitable for general prototyping and functional testing.
- Dental and Medical Resins: Resins with biocompatible properties are specifically formulated for dental and medical applications, such as surgical guides, orthodontic models, and anatomical models.
- Transparent Resins: These resins provide excellent optical clarity, making them ideal for applications that require transparency, such as lenses, light guides, and consumer products.
- Elastic Resins: Resins with flexible properties cater to applications that demand elasticity, such as custom grips, gaskets, and wearable devices.
Applications of Stereolithography
The versatility of stereolithography opens up a wide array of applications across various industries, transforming the way products are designed and manufactured.
Stereolithography in Manufacturing
In the manufacturing sector, stereolithography finds applications in rapid prototyping, tooling, and custom manufacturing. It allows designers and engineers to iterate their designs quickly, reducing time and cost associated with traditional prototyping methods. Additionally, the ability to create complex geometries in a single print helps optimize tooling production, leading to improved efficiency and cost savings.
Stereolithography also plays a vital role in end-use production. With advancements in materials and process control, it is now possible to produce final parts with the required mechanical properties, enabling small-batch and on-demand manufacturing.
Stereolithography in Medicine and Dentistry
Medicine and dentistry have greatly benefitted from the advancements in stereolithography. In dentistry, stereolithography is used to create highly accurate dental models, orthodontic appliances, surgical guides, and customized dental implants. The ability to produce patient-specific models and devices allows for better treatment planning and improved patient outcomes.
In medicine, stereolithography enables the creation of anatomical models for preoperative planning, patient-specific surgical guides, and even customized implants. This technology has revolutionized procedures such as reconstructive surgery, orthopedics, and maxillofacial surgery, enhancing precision and reducing surgical risks.
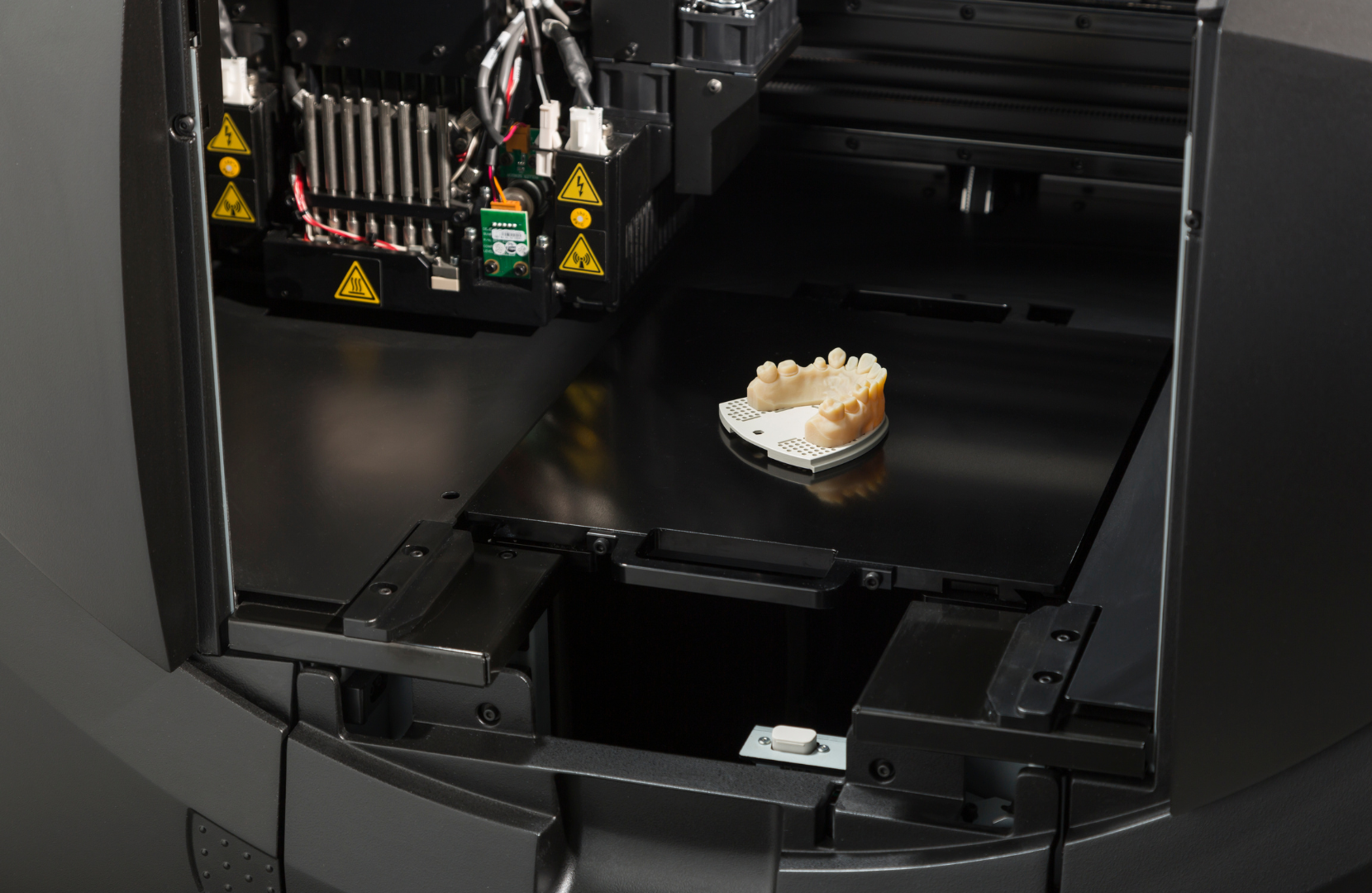
Future Trends in Stereolithography
As with any technology, stereolithography continues to evolve, presenting new possibilities and future trends.
Innovations and Developments in Stereolithography
Stereolithography is a rapidly advancing technology, and researchers and engineers are continuously exploring new materials, process improvements, and hardware advancements to enhance its capabilities. Innovations such as more environmentally friendly resins, higher printing speeds, and larger build sizes are being pursued to expand the reach of stereolithography and make it even more cost-effective.
The Impact of Stereolithography on Future 3D Printing Technologies
While other 3D printing technologies, such as selective laser sintering (SLS) and fused deposition modeling (FDM), have gained popularity, stereolithography remains a significant player thanks to its high precision and surface quality. Its ability to produce parts with fine details and intricate geometries gives it a unique advantage in certain applications, ensuring its place in the future of 3D printing.
Furthermore, the advancements in stereolithography are also influencing other technologies. The integration of real-time monitoring, automated support generation, and improved post-processing techniques are being adopted by other 3D printing methods, further enhancing their capabilities and user experience.
Understanding the heart of 3D printing, stereolithography, is crucial for anyone interested in the field of additive manufacturing. Its history, process, and applications provide valuable insights into the incredible potential of this technology. With continuous innovations and advancements, stereolithography is set to shape the future of manufacturing, enabling new levels of design complexity, customization, and efficiency.