La impresión 3D ha revolucionado la fabricación al permitir la creación de objetos complejos y personalizados mediante la fabricación aditiva capa a capa. Aunque el plástico ha sido el material elegido para muchas aplicaciones de impresión 3D, los avances recientes han allanado el camino para la exploración de una amplia gama de materiales. En este artículo, profundizaremos en las limitaciones del plástico en la impresión 3D y exploraremos el potencial de materiales alternativos como el metal, la cerámica, los compuestos y los biomateriales.
Comprender las limitaciones del plástico en la impresión 3D
El plástico ha sido ampliamente adoptado en la impresión 3D debido a su asequibilidad, accesibilidad y facilidad de impresión. Sin embargo, su uso tiene limitaciones que no se pueden ignorar.
Impacto ambiental del uso de plásticos
Unade las principales preocupaciones del plástico es su impacto en el medio ambiente. Se sabe que los residuos plásticos persisten en el medio ambiente durante cientos de años, contribuyendo a la contaminación, la saturación de los vertederos y el daño a la vida marina. A medida que la sostenibilidad adquiere protagonismo, la necesidad de ir más allá del plástico se hace cada vez más crucial.
La contaminación por plásticos se ha convertido en una crisis mundial, con millones de toneladas de residuos plásticos que acaban en nuestros océanos cada año. Estos residuos no sólo suponen una amenaza para la vida marina, sino que también entran en la cadena alimentaria, perjudicando potencialmente la salud humana. La acumulación de residuos plásticos en los vertederos también contribuye a las emisiones de gases de efecto invernadero, agravando el cambio climático.
La durabilidad y resistencia del plástico
Otralimitación del plástico en la impresión 3D es su durabilidad y resistencia. Aunque el plástico es adecuado para muchas aplicaciones, puede no poseer las propiedades mecánicas necesarias para las tareas más exigentes. Esto puede plantear problemas en sectores en los que la resistencia y la durabilidad son fundamentales, como el aeroespacial y el de la automoción.
En la industria aeroespacial, por ejemplo, los componentes deben soportar condiciones extremas, como altas temperaturas e intensas vibraciones. Aunque algunos plásticos pueden cumplir estos requisitos, a menudo necesitan refuerzos o revestimientos adicionales para mejorar su resistencia y durabilidad. Esto añade complejidad y coste al proceso de fabricación.
Del mismo modo, la industria del automóvil depende de materiales resistentes y duraderos para garantizar la seguridad y longevidad de los vehículos. Mientras que los componentes de plástico se pueden encontrar en varias partes de un coche, como las molduras interiores y los parachoques, los componentes estructurales críticos a menudo requieren materiales con mayor fuerza y resistencia al impacto, como los metales o los compuestos.
Abordar las limitaciones del plástico en la impresión 3D es un reto constante para investigadores e ingenieros. Se están realizando esfuerzos para desarrollar nuevos materiales que ofrezcan propiedades mecánicas mejoradas manteniendo las ventajas de asequibilidad y accesibilidad que proporciona el plástico. Estos avances no sólo ampliarán la gama de aplicaciones de la impresión 3D, sino que también contribuirán a un futuro más sostenible y resistente.
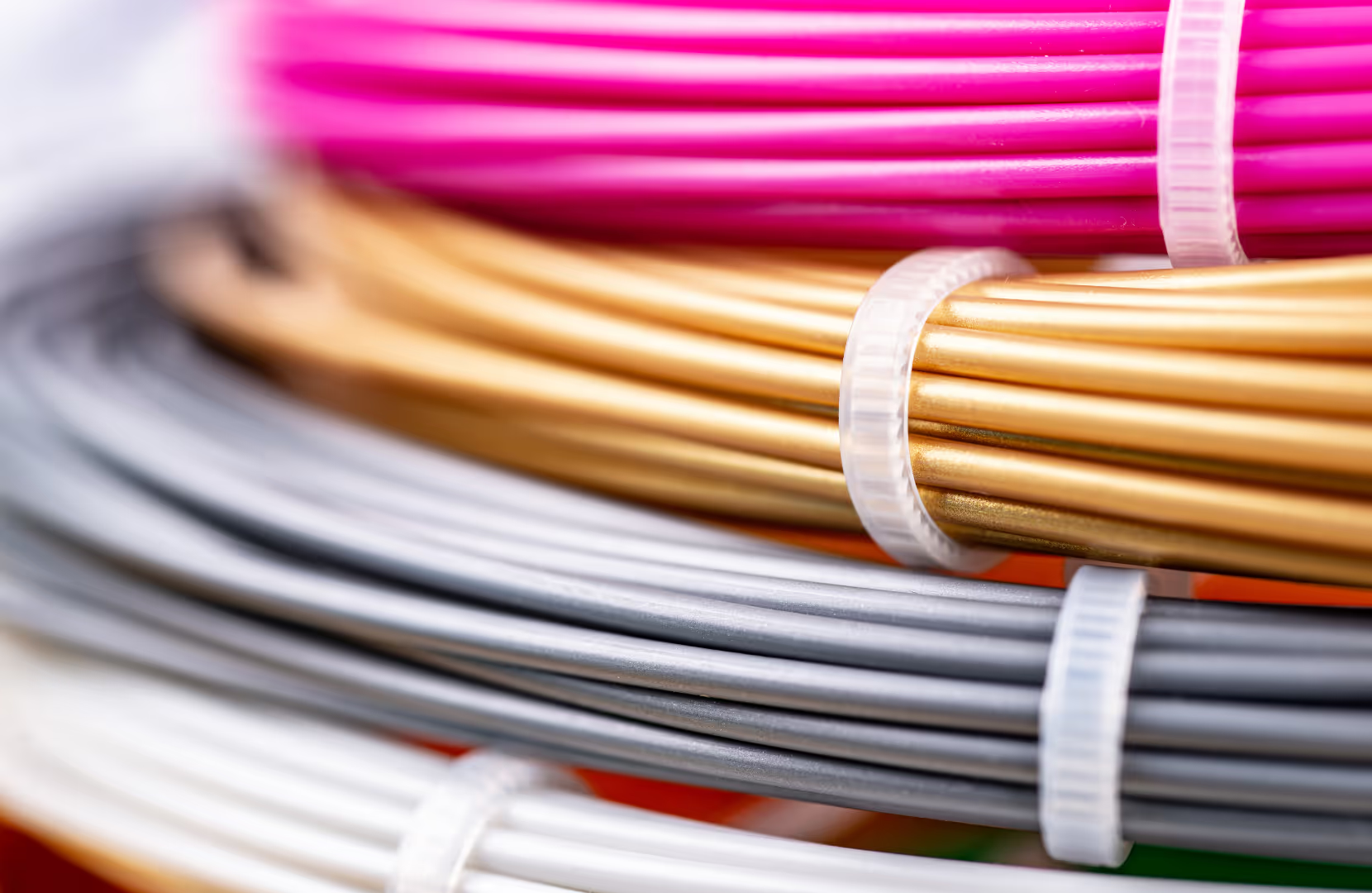
Exploración del potencial del metal en la impresión 3D
Los materiales metá licos constituyen una prometedora alternativa al plástico en la impresión 3D, ya que ofrecen ventajas y capacidades únicas. La versatilidad de los materiales metálicos abre un mundo de posibilidades en el ámbito de la fabricación aditiva.
La versatilidad de los materiales metálicos
Losmetales ofrecen una resistencia y durabilidad superiores a las del plástico, por lo que son ideales para aplicaciones que requieren un alto rendimiento e integridad estructural. Con la impresión 3D en metal se pueden conseguir geometrías complejas, lo que permite crear piezas intrincadas y personalizadas.
Una de las principales ventajas de utilizar metal en la impresión 3D es la capacidad de crear estructuras ligeras pero resistentes. Esto es especialmente beneficioso en industrias como la aeroespacial y la automovilística, donde la reducción de peso es crucial para mejorar la eficiencia del combustible y el rendimiento general. La impresión 3D en metal permite producir estructuras reticulares complejas y componentes huecos, que pueden reducir considerablemente el peso manteniendo la integridad estructural.
Además, los materiales metálicos ofrecen una excelente conductividad térmica y eléctrica, lo que los hace idóneos para aplicaciones en electrónica y transferencia de calor. Gracias a la impresión 3D de metales, los ingenieros pueden diseñar y fabricar disipadores de calor, conectores eléctricos y otros componentes que requieren una gestión térmica o una conductividad eléctrica eficientes.
Los retos del uso del metal en la impresión 3D
Sin embargo, la impresión 3D en metal plantea algunas dificultades. Los metales tienen puntos de fusión más altos y requieren técnicas y equipos de impresión especializados. El proceso de impresión 3D de metales, también conocido como sinterizado directo de metales por láser (DMLS) o fusión selectiva por láser (SLM), consiste en fundir el polvo metálico capa por capa mediante un láser de alta potencia. Esto requiere un control preciso de los parámetros del láser, como la potencia, la velocidad y el enfoque, para garantizar la fusión adecuada del polvo metálico.
Además de los retos técnicos, también hay que tener en cuenta los pasos de posprocesamiento necesarios para las piezas metálicas impresas en 3D. Tras la impresión, las piezas metálicas suelen requerir tratamiento térmico para aliviar las tensiones residuales y mejorar las propiedades mecánicas. También puede ser necesario el mecanizado para conseguir tolerancias estrechas o acabados superficiales suaves. Estos pasos de posprocesamiento añaden complejidad y coste a la producción, por lo que la impresión 3D en metal es un proceso más complejo que la impresión 3D en plástico.
A pesar de estos retos, el potencial del metal en la impresión 3D es innegable. A medida que avanza la tecnología y se llevan a cabo más investigaciones, se van abordando las limitaciones de la impresión 3D en metal, allanando el camino para una adopción y aplicación más amplias de esta innovadora técnica de fabricación.
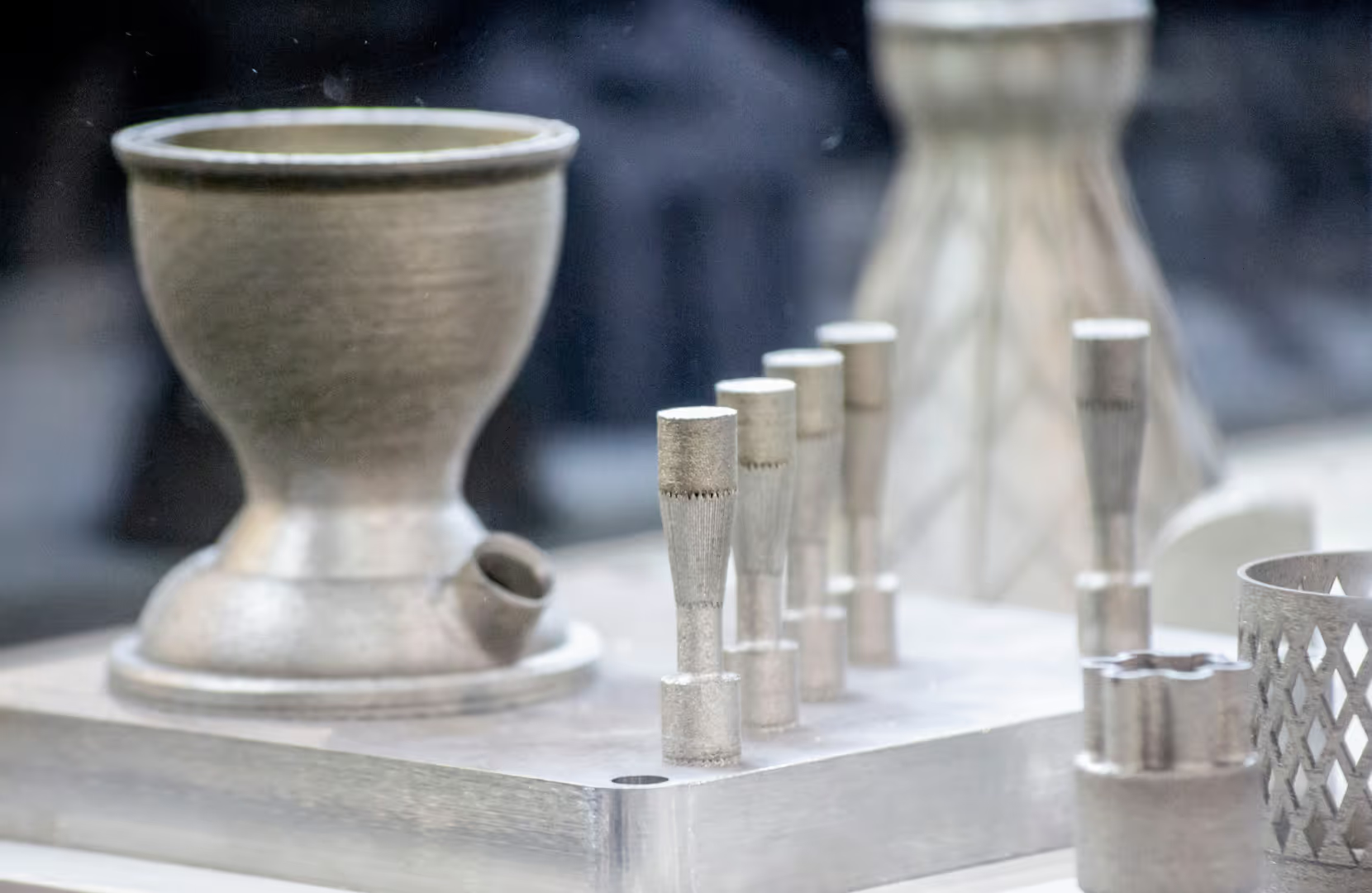
La aparición de la cerámica en la impresión 3D
Los materiales cerámicos ofrecen un conjunto único de propiedades que los hacen muy atractivos para determinadas aplicaciones. Gracias a su excelente resistencia al calor, alta estabilidad química y propiedades de aislamiento eléctrico, la cerámica se ha convertido en un material muy solicitado en sectores como el aeroespacial, la electrónica y la medicina. La aparición de la cerámica en la impresión 3D ha abierto nuevas posibilidades para crear componentes cerámicos intrincados y personalizados.
Las propiedades únicas de la cerámica
Lacerámica posee una notable combinación de propiedades que la distinguen de otros materiales. Su excepcional resistencia al calor permite a la cerámica soportar temperaturas extremas, lo que la hace ideal para aplicaciones en motores a reacción, turbinas de gas y otros entornos de alta temperatura. Además, la cerámica presenta una gran estabilidad química, lo que le permite resistir la corrosión y la degradación causadas por productos químicos agresivos. Esta propiedad hace que la cerámica sea idónea para su uso en plantas de procesamiento químico y dispositivos biomédicos. Además, los materiales cerámicos son excelentes aislantes eléctricos, lo que los hace indispensables en componentes y circuitos electrónicos.
Los posibles inconvenientes de la cerámica en la impresión 3D
Apesar de las numerosas ventajas de los materiales cerámicos, su integración en el ámbito de la impresión 3D presenta retos únicos. Una de las principales preocupaciones es la fragilidad inherente de la cerámica, que la hace propensa a agrietarse y romperse. Esta fragilidad plantea dificultades durante el proceso de impresión, ya que cualquier ligera manipulación o tensión puede provocar fallos estructurales. Para solucionar este problema, investigadores e ingenieros exploran continuamente enfoques innovadores para mejorar las propiedades mecánicas de los objetos cerámicos impresos en 3D.
Otra complejidad asociada a la impresión cerámica en 3D es la necesidad de controlar con precisión diversos parámetros. La regulación de la temperatura es fundamental para garantizar una sinterización y unión adecuadas de las partículas cerámicas. El entorno de impresión debe controlarse cuidadosamente para evitar el enfriamiento o calentamiento rápidos, que pueden provocar defectos y una adhesión débil entre capas. Además, la humedad desempeña un papel crucial en la impresión cerámica en 3D, ya que un exceso de humedad puede provocar una mala fluidez del material y comprometer la integridad estructural. Lograr una distribución óptima del tamaño de las partículas también es crucial para obtener impresiones cerámicas de alta calidad, ya que una dispersión inadecuada de las partículas puede dar lugar a una distribución irregular del material y comprometer las propiedades mecánicas.
A pesar de estos retos, el potencial de la impresión cerámica en 3D es inmenso. La capacidad de fabricar estructuras cerámicas complejas con geometrías intrincadas abre nuevas vías para el diseño y la innovación. Las posibilidades son enormes: desde implantes dentales cerámicos complejos hasta componentes cerámicos ligeros para aplicaciones aeroespaciales. Investigadores y expertos del sector trabajan activamente para superar las limitaciones de la impresión cerámica en 3D y ampliar las posibilidades de esta fascinante tecnología.
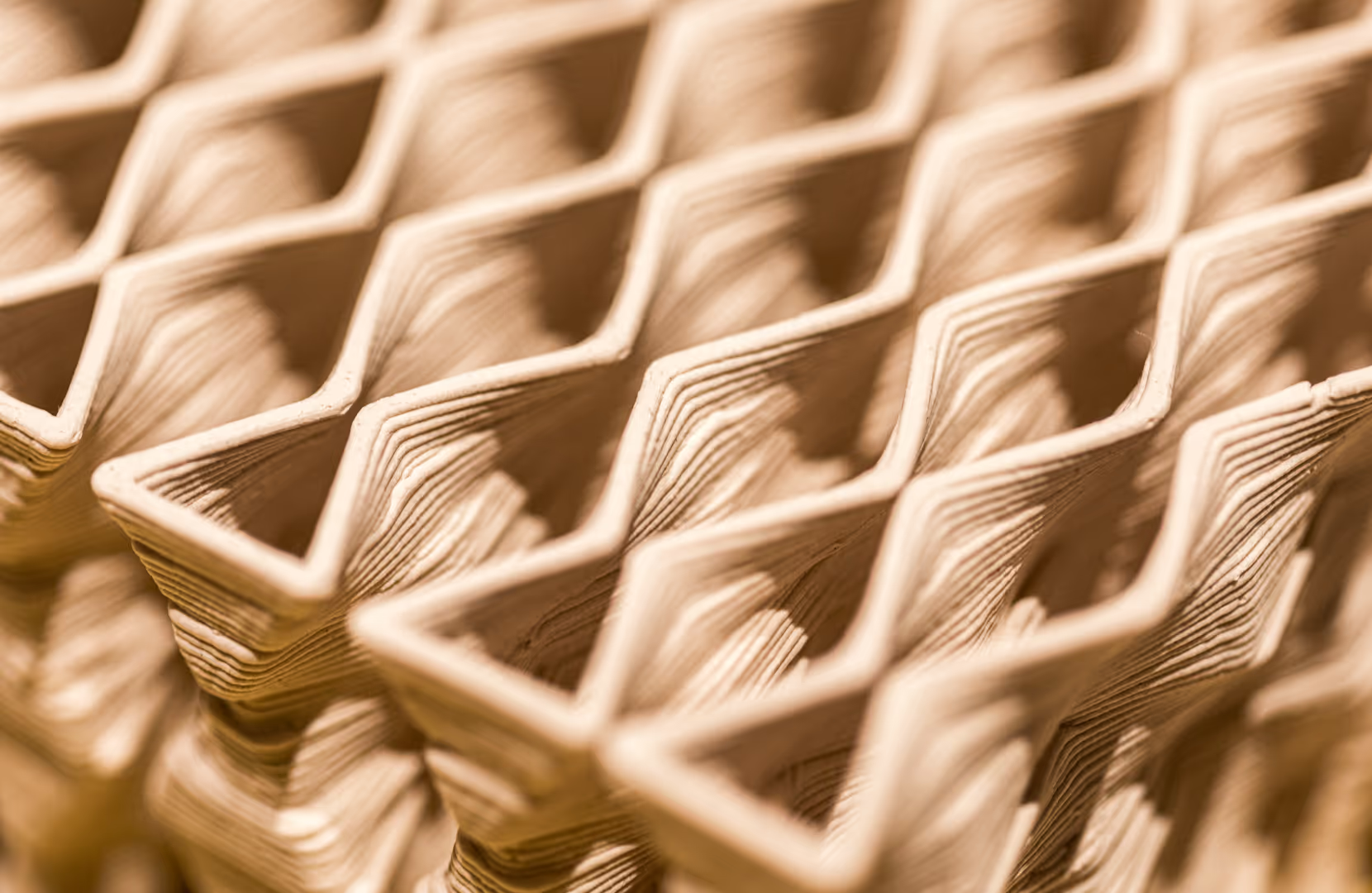
El papel de los composites en la impresión 3D
Los materiales compuestos ofrecen una combinación única de propiedades al combinar dos o más materiales distintos en una única estructura.
Resistencia y ligereza de los materiales compuestos
Losmateriales compuestos presentan una notable relación resistencia-peso, lo que los hace ideales para diversas aplicaciones en las que la reducción de peso es crucial sin comprometer la integridad estructural. Industrias como la aeroespacial, la automovilística y la de equipamiento deportivo pueden beneficiarse enormemente del uso de materiales compuestos en la impresión 3D.
La complejidad de imprimir con materiales compuestos
Sinembargo, la impresión con materiales compuestos introduce complejidades como la compatibilidad de materiales, la orientación de las fibras y la adherencia fiable entre capas. Estos retos exigen una cuidadosa optimización de los parámetros de impresión y el desarrollo de técnicas de impresión especializadas.
El futuro de los biomateriales en la impresión 3D
Los biomateriales, derivados de fuentes naturales o sintéticas, ofrecen interesantes posibilidades para las aplicaciones de impresión 3D.
La sostenibilidad de los biomateriales
Losbiomateriales ofrecen una alternativa sostenible a los materiales tradicionales al utilizar recursos renovables y reducir la dependencia de los combustibles fósiles. Esto coincide con la creciente demanda de prácticas de fabricación respetuosas con el medio ambiente.
Retos y potencial de los biomateriales en la impresión 3D
Sinembargo, hay retos que superar con los biomateriales, como garantizar unas propiedades mecánicas adecuadas, la biocompatibilidad y el cumplimiento de la normativa para aplicaciones médicas. La investigación y el desarrollo continuos son necesarios para liberar todo el potencial de los biomateriales en la impresión 3D.
Conclusión
A medida que la impresión 3D sigue evolucionando, también lo hace la gama de materiales disponibles para su uso. Aunque el plástico ha desempeñado un papel importante en la revolución de la impresión 3D, la exploración de diversos materiales como el metal, la cerámica, los compuestos y los biomateriales abre nuevas vías de innovación y aplicación. Cada material presenta sus propias ventajas y desafíos, por lo que se debe prestar especial atención a la selección del material adecuado para cada necesidad. Al adoptar diversos materiales en la impresión 3D, podemos desbloquear posibilidades ilimitadas y dar forma a un futuro sostenible en la fabricación.