3D printing has revolutionized manufacturing by allowing for the creation of complex and customized objects using layer-by-layer additive manufacturing. While plastic has been the material of choice for many 3D printing applications, recent advancements have paved the way for the exploration of a wide range of materials. In this article, we will delve into the limitations of plastic in 3D printing and explore the potential of alternative materials such as metal, ceramic, composites, and bio-materials.
โ
Understanding the Limitations of Plastic in 3D Printing
โ
Plastic has been widely adopted in 3D printing due to its affordability, accessibility, and ease of printing. However, there are limitations to its use that cannot be ignored.
โ
The Environmental Impact of Plastic Use
โ
โOne major concern with plastic is its impact on the environment. Plastic waste is known to persist in the environment for hundreds of years, contributing to pollution, landfill overcrowding, and harm to marine life. As sustainability takes center stage, the need to move beyond plastic becomes ever more crucial.
โ
Plastic pollution has become a global crisis, with millions of tons of plastic waste ending up in our oceans each year. This waste not only poses a threat to marine life but also enters the food chain, potentially harming human health. The accumulation of plastic waste in landfills also contributes to greenhouse gas emissions, exacerbating climate change.
โ
The Durability and Strength Concerns of Plastic
โ
โAnother limitation of plastic in 3D printing is its durability and strength. While plastic is suitable for many applications, it may not possess the required mechanical properties for more demanding tasks. This can pose challenges for industries where strength and durability are critical, such as aerospace and automotive.
โ
In the aerospace industry, for example, components need to withstand extreme conditions, including high temperatures and intense vibrations. While some plastics can meet these requirements, they often require additional reinforcements or coatings to enhance their strength and durability. This adds complexity and cost to the manufacturing process.
โ
Similarly, the automotive industry relies on strong and durable materials to ensure the safety and longevity of vehicles. While plastic components can be found in various parts of a car, such as interior trims and bumpers, critical structural components often require materials with higher strength and impact resistance, such as metals or composites.
โ
Addressing the limitations of plastic in 3D printing is an ongoing challenge for researchers and engineers. Efforts are being made to develop new materials that offer improved mechanical properties while maintaining the benefits of affordability and accessibility that plastic provides. These advancements will not only expand the range of applications for 3D printing but also contribute to a more sustainable and resilient future.
โ
โ
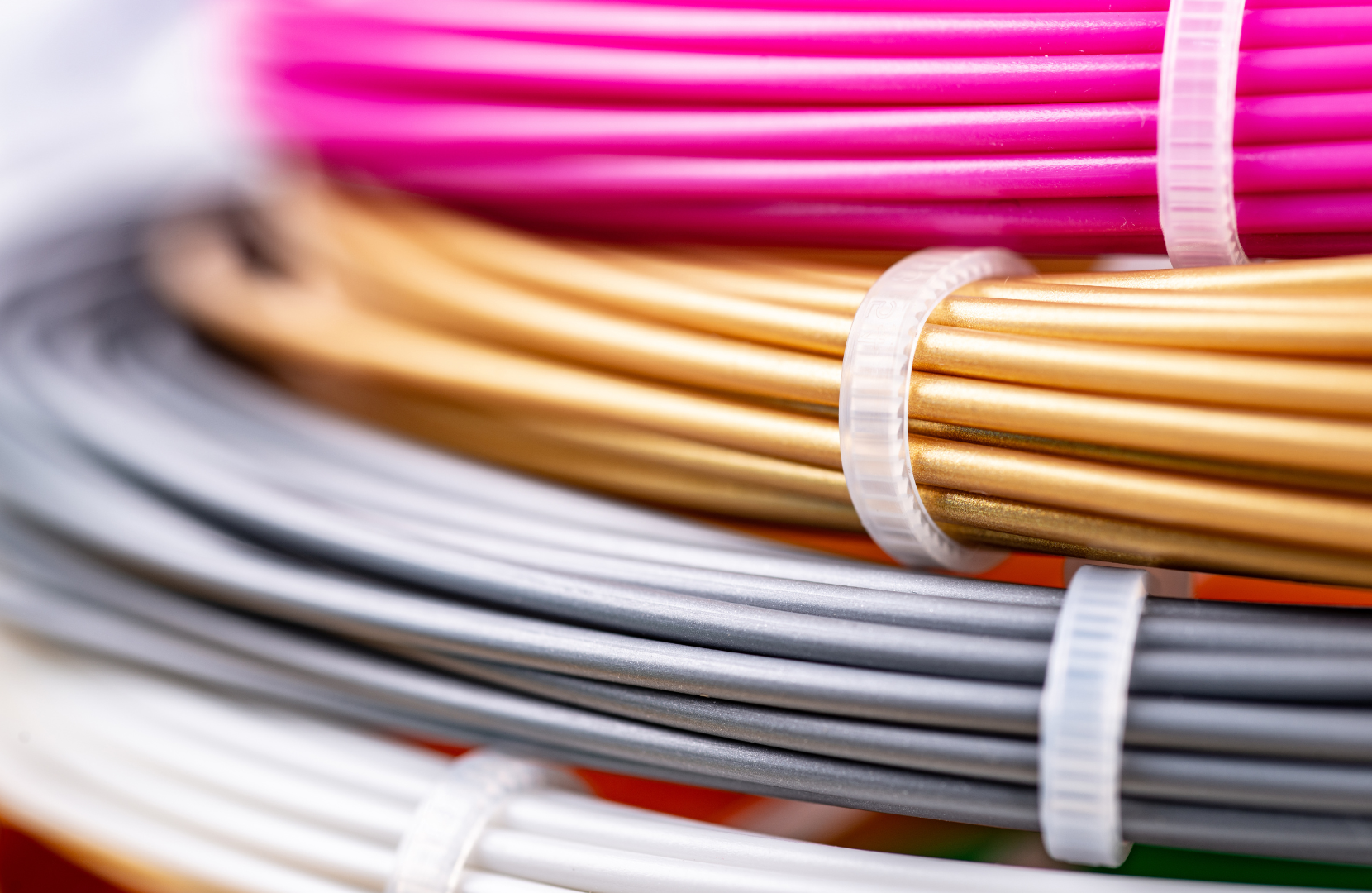
โ
โ
Exploring the Potential of Metal in 3D Printing
โ
Metal materials provide a promising alternative to plastic in 3D printing, offering unique advantages and capabilities. The versatility of metal materials opens up a world of possibilities in the realm of additive manufacturing.
โ
The Versatility of Metal Materials
โ
โMetals provide superior strength and durability compared to plastic, making them ideal for applications that require high-performance and structural integrity. With metal 3D printing, complex geometries can be achieved, enabling the creation of intricate and customized parts.
โ
One of the key advantages of using metal in 3D printing is the ability to create lightweight yet strong structures. This is particularly beneficial in industries such as aerospace and automotive, where weight reduction is crucial for improving fuel efficiency and overall performance. Metal 3D printing allows for the production of complex lattice structures and hollow components, which can significantly reduce weight while maintaining structural integrity.
โ
Furthermore, metal materials offer excellent thermal and electrical conductivity, making them suitable for applications in electronics and heat transfer. By leveraging metal 3D printing, engineers can design and fabricate intricate heat sinks, electrical connectors, and other components that require efficient thermal management or electrical conductivity.
โ
The Challenges of Using Metal in 3D Printing
โ
โHowever, there are challenges associated with metal 3D printing. Metals have higher melting points and require specialized printing techniques and equipment. The process of metal 3D printing, also known as direct metal laser sintering (DMLS) or selective laser melting (SLM), involves melting metal powder layer by layer using a high-powered laser. This requires precise control of laser parameters, such as power, speed, and focus, to ensure proper melting and fusion of the metal powder.
โ
In addition to the technical challenges, there are also considerations regarding the post-processing steps required for metal 3D printed parts. After printing, metal parts often require heat treatment to relieve residual stresses and improve mechanical properties. Machining may also be necessary to achieve tight tolerances or smooth surface finishes. These post-processing steps add to the complexity and cost of production, making metal 3D printing a more involved process compared to plastic 3D printing.
โ
Despite these challenges, the potential of metal in 3D printing is undeniable. As technology advances and more research is conducted, the limitations of metal 3D printing are being addressed, paving the way for wider adoption and application of this innovative manufacturing technique.
โ
โ
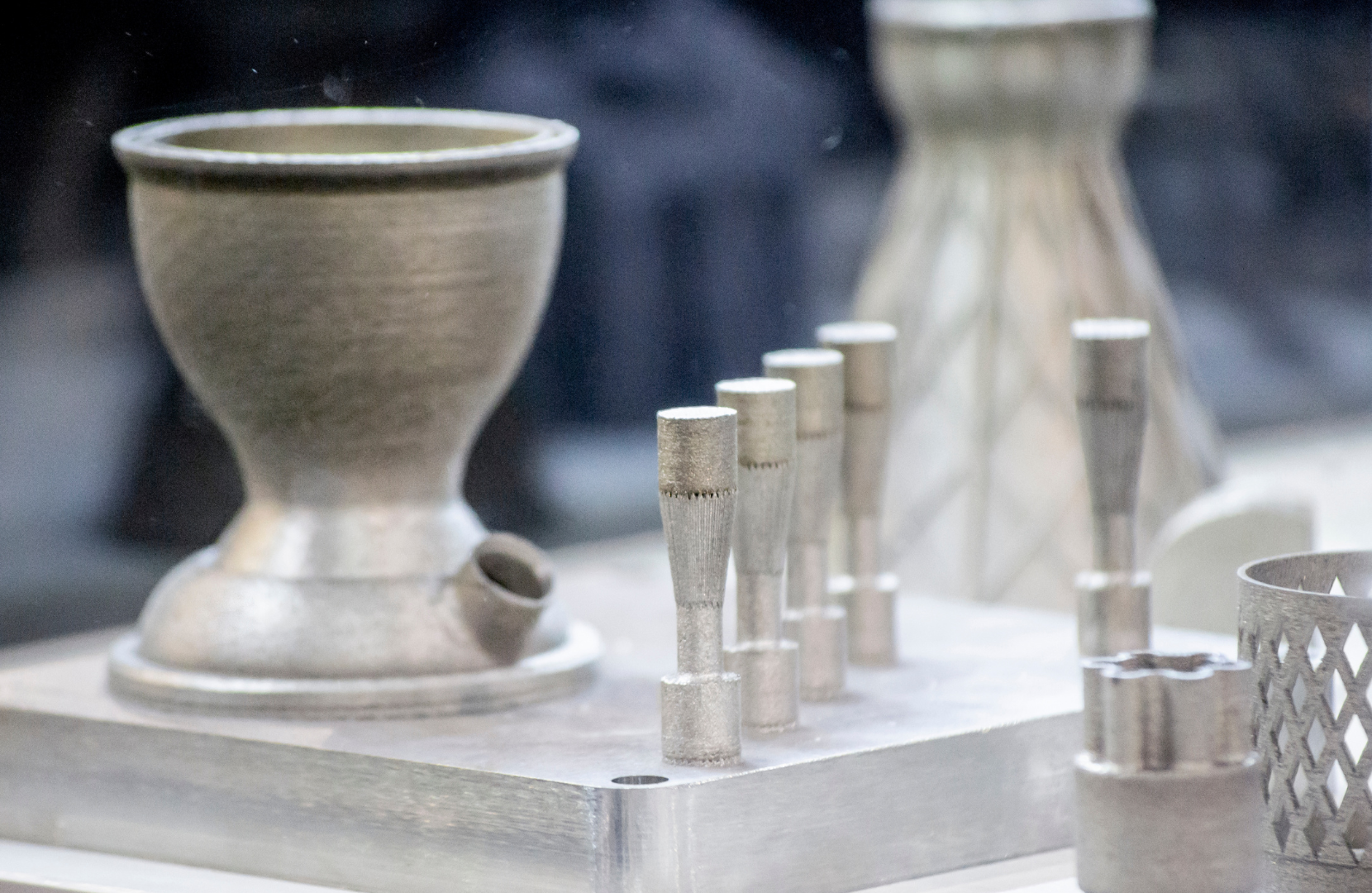
โ
โ
The Emergence of Ceramic in 3D Printing
โ
Ceramic materials offer a unique set of properties that make them highly attractive for certain applications. With their excellent heat resistance, high chemical stability, and electrical insulation properties, ceramics have become a sought-after material in industries such as aerospace, electronics, and medicine. The emergence of ceramic in 3D printing has opened up new possibilities for creating intricate and customized ceramic components.
โ
The Unique Properties of Ceramic
โ
โCeramics possess a remarkable combination of properties that set them apart from other materials. Their exceptional heat resistance allows ceramics to withstand extreme temperatures, making them ideal for applications in jet engines, gas turbines, and other high-temperature environments. Additionally, ceramics exhibit high chemical stability, enabling them to resist corrosion and degradation caused by harsh chemicals. This property makes ceramics well-suited for use in chemical processing plants and biomedical devices. Furthermore, ceramics are excellent electrical insulators, making them indispensable in electronic components and circuitry.
โ
The Potential Drawbacks of Ceramic in 3D Printing
โ
โDespite the numerous advantages of ceramic materials, their integration into the realm of 3D printing presents unique challenges. One of the primary concerns is the inherent brittleness of ceramics, which makes them prone to cracking and breakage. This fragility poses difficulties during the printing process, as any slight mishandling or stress can lead to structural failures. To address this issue, researchers and engineers are continuously exploring innovative approaches to enhance the mechanical properties of ceramic 3D printed objects.
โ
Another complexity associated with ceramic 3D printing is the need for precise control over various parameters. Temperature regulation is critical to ensure proper sintering and bonding of ceramic particles. The printing environment must be carefully controlled to prevent rapid cooling or heating, which can result in defects and weak interlayer adhesion. Additionally, humidity plays a crucial role in ceramic 3D printing, as excessive moisture can lead to poor material flow and compromised structural integrity. Achieving the optimal particle size distribution is also crucial for obtaining high-quality ceramic prints, as improper particle dispersion can result in uneven material distribution and compromised mechanical properties.
โ
Despite these challenges, the potential of ceramic 3D printing is immense. The ability to fabricate complex ceramic structures with intricate geometries opens up new avenues for design and innovation. From intricate ceramic dental implants to lightweight ceramic components for aerospace applications, the possibilities are vast. Researchers and industry experts are actively working towards overcoming the limitations of ceramic 3D printing, pushing the boundaries of what can be achieved with this fascinating technology.
โ
โ

โ
โ
The Role of Composites in 3D Printing
โ
Composites offer a unique combination of properties by combining two or more distinct materials into a single structure.
โ
The Strength and Lightweight Nature of Composites
โ
โComposites exhibit remarkable strength-to-weight ratios, making them ideal for various applications where weight reduction is crucial without compromising structural integrity. Industries such as aerospace, automotive, and sports equipment can greatly benefit from the use of composite materials in 3D printing.
โ
The Complexities of Printing with Composites
โ
โHowever, printing with composites introduces complexities such as material compatibility, fiber orientation, and reliable adhesion between layers. These challenges require careful optimization of printing parameters and the development of specialized printing techniques.
โ
The Future of Bio-materials in 3D Printing
โ
Bio-materials, derived from natural or synthetic sources, offer exciting possibilities for 3D printing applications.
โ
The Sustainability of Bio-material
โ
โBio-materials provide a sustainable alternative to traditional materials by utilizing renewable resources and reducing dependence on fossil fuels. This aligns with the growing demand for environmentally friendly manufacturing practices.
โ
The Challenges and Potential of Bio-materials in 3D Printing
โ
โHowever, there are challenges to overcome with bio-materials, such as ensuring suitable mechanical properties, biocompatibility, and regulatory compliance for medical applications. Ongoing research and development are necessary to unlock the full potential of bio-materials in 3D printing.
โ
Conclusion
โ
As 3D printing continues to evolve, so does the range of materials available for use. While plastic has played a significant role in the 3D printing revolution, exploring diverse materials such as metal, ceramic, composites, and bio-materials opens up new avenues for innovation and application. Each material brings its unique set of advantages and challenges, and careful consideration must be given to selecting the right material for specific requirements. By embracing diverse materials in 3D printing, we can unlock limitless possibilities and shape a sustainable future in manufacturing.