In today's rapidly evolving technological landscape, the Internet of Things (IoT) has emerged as a game-changer in various industries. Manufacturing, in particular, has seen significant transformations with the integration of IoT into its processes. This article explores the concept of IoT and its evolution, as well as its role in the manufacturing sector. Furthermore, it delves into the benefits of incorporating IoT in manufacturing, providing real-world examples to highlight its impact. Lastly, it examines the challenges of implementing IoT in manufacturing and proposes solutions to overcome them.
Understanding the Internet of Things (IoT)
Before delving into the specifics, it is essential to understand the basics of the Internet of Things. Simply put, IoT refers to the interconnectivity of physical devices that collect and exchange data through the internet. These devices, equipped with sensors and software, can communicate and interact with each other without human intervention. This ability to seamlessly exchange information has opened up a world of possibilities, particularly in the manufacturing domain.
Definition of IoT
IoT can be defined as a network of interconnected devices, embedded with sensors and software, that collect and exchange data through the internet.
The Evolution of IoT
The concept of IoT has evolved over the years, driven by advancements in technology and the increasing need for connectivity. Initially, IoT was focused on connecting computers and smartphones. However, with the advent of sensors and the miniaturization of computing devices, IoT expanded to include a wide range of "smart" devices. These devices include wearables, home appliances, vehicles, and industrial machinery. The ability of these devices to connect and communicate has enabled the emergence of smart manufacturing, often referred to as Industry 4.0.
Industry 4.0 represents the fourth industrial revolution, characterized by the integration of digital technologies into manufacturing processes. With the advent of IoT, factories are becoming smarter and more efficient. Machines equipped with sensors can monitor their own performance and communicate with other machines in the production line. This enables real-time data analysis and predictive maintenance, leading to reduced downtime and increased productivity.
In addition to manufacturing, IoT has also made a significant impact in the healthcare industry. Connected medical devices, such as wearable fitness trackers and remote patient monitoring systems, allow healthcare professionals to remotely monitor patients' vital signs and provide timely interventions. This not only improves patient outcomes but also reduces the burden on healthcare systems by minimizing hospital readmissions.
Furthermore, IoT has transformed the way we live in our homes. Smart home devices, such as thermostats, lighting systems, and security cameras, can be controlled remotely through smartphones or voice assistants. This level of automation and convenience enhances energy efficiency, home security, and overall comfort.
Another area where IoT is revolutionizing is transportation. Connected vehicles equipped with IoT technology can communicate with each other and with roadside infrastructure, enabling real-time traffic management and accident prevention. Additionally, IoT plays a crucial role in logistics and supply chain management, optimizing routes, tracking shipments, and minimizing delays.
As IoT continues to evolve, its potential applications are limitless. From agriculture to energy management, from retail to environmental monitoring, IoT has the power to transform industries and improve our daily lives. The interconnectivity of devices and the abundance of data generated by IoT present exciting opportunities for innovation and growth in the digital era.
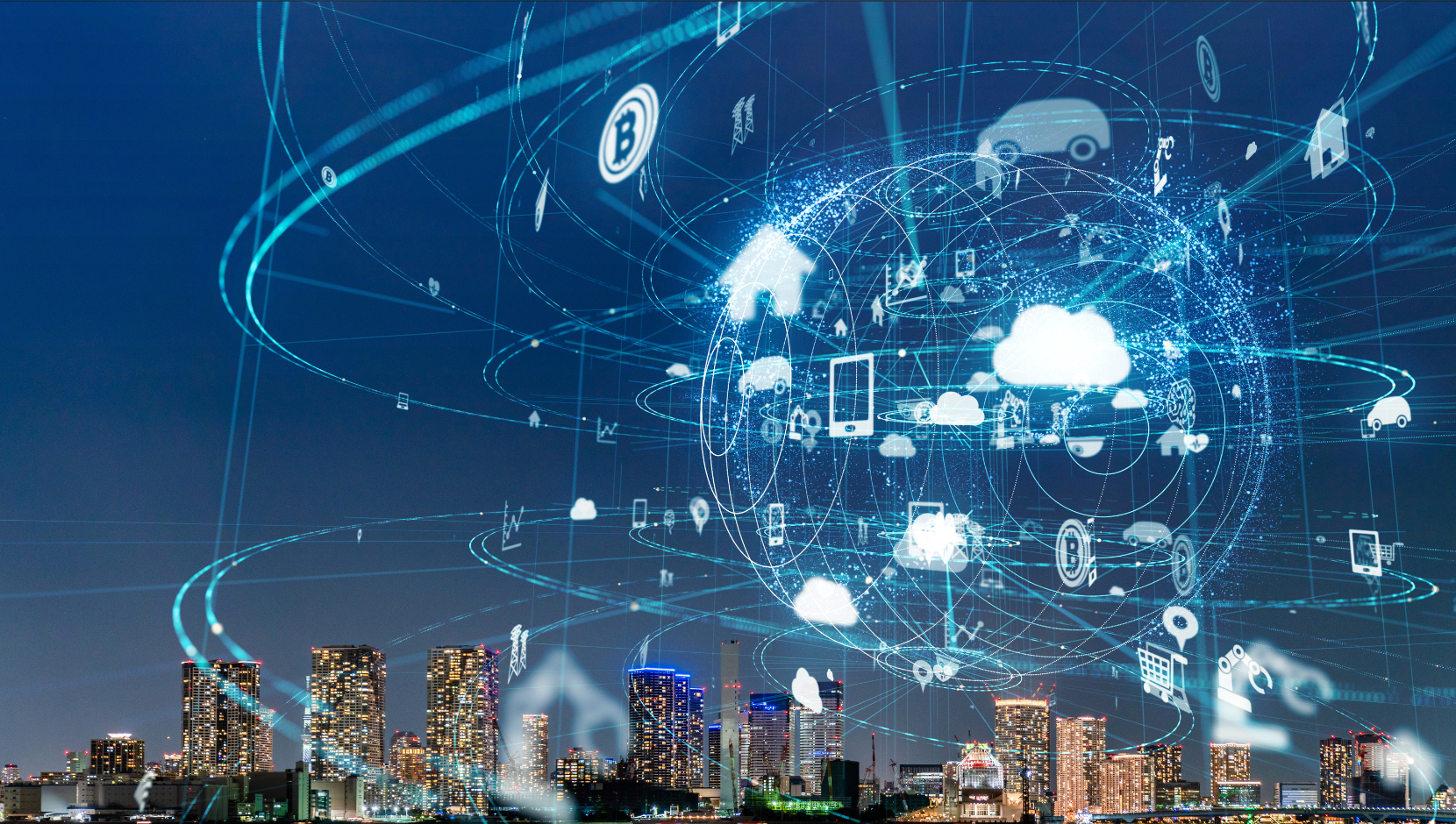
The Role of IoT in Manufacturing
IoT has revolutionized the manufacturing sector by streamlining processes, improving efficiency, and enhancing overall productivity. Let's explore some specific areas where IoT has made a significant impact in manufacturing.
IoT in Production Lines
One of the key areas where IoT has transformed manufacturing is in production lines. By deploying IoT-enabled sensors throughout the production line, manufacturers can collect real-time data on various parameters such as temperature, pressure, and speed. This data can be analyzed to identify bottlenecks, optimize production schedules, and predict maintenance requirements. With this level of insight, manufacturers can improve their production processes by minimizing downtime and maximizing output.
For example, imagine a car manufacturing plant that utilizes IoT sensors throughout its production line. These sensors can monitor the temperature of welding machines, the pressure of hydraulic systems, and the speed of conveyor belts. The data collected from these sensors can be analyzed to identify any deviations from the optimal operating conditions. If a welding machine is running at a higher temperature than usual, it could indicate a potential issue that needs to be addressed. By detecting such anomalies in real-time, manufacturers can take immediate action to prevent any production delays or quality issues.
In addition to monitoring individual components, IoT can also enable a holistic view of the entire production line. By collecting data from multiple sensors, manufacturers can gain insights into the overall performance of the production line. For instance, they can identify which stages of the production process are causing delays or bottlenecks, allowing them to make informed decisions to optimize the flow of operations.
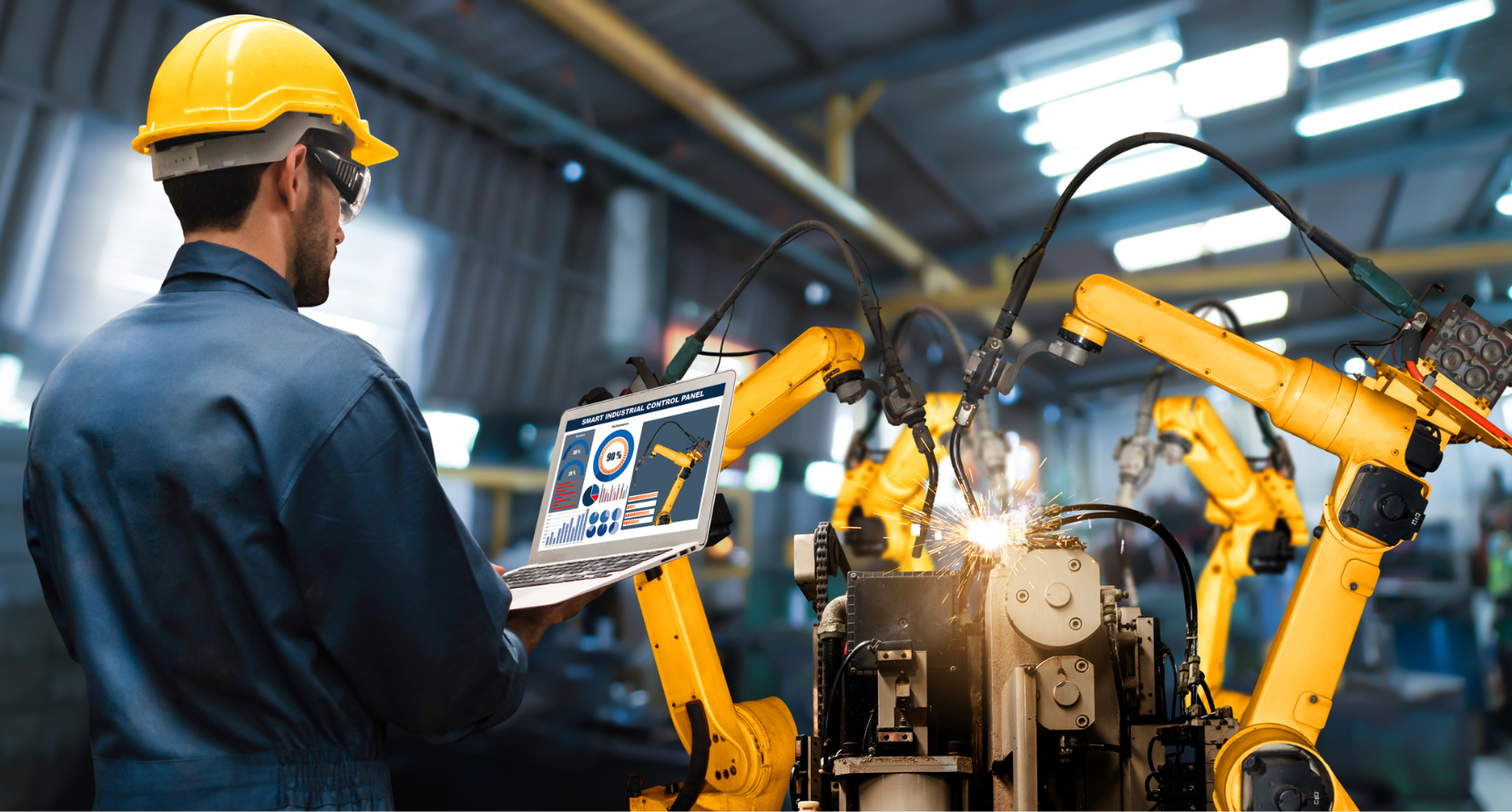
IoT in Quality Control
Quality control is a critical aspect of manufacturing, ensuring that products meet the required standards. IoT plays a crucial role in enhancing quality control by continuously monitoring and analyzing data from production processes. Sensors can detect anomalies or deviations from the desired specifications, triggering alerts for immediate action. Furthermore, IoT-enabled devices can monitor the performance of individual components or equipment, enabling proactive maintenance and reducing the likelihood of defective products reaching customers.
To illustrate this, let's consider a food processing plant that utilizes IoT sensors to monitor the temperature and humidity levels in their storage facilities. These sensors can continuously collect data and compare it to the ideal conditions for storing perishable goods. If the temperature or humidity deviates from the desired range, the sensors can send alerts to the quality control team, allowing them to take corrective action before any products are compromised. This proactive approach not only ensures the quality and safety of the products but also minimizes the risk of costly product recalls.
Moreover, IoT can also enable real-time monitoring of product quality during the manufacturing process. For example, sensors can measure the dimensions of a product or conduct automated tests to check for defects. Any deviations from the predefined quality standards can trigger immediate alerts, allowing manufacturers to take corrective measures and prevent the production of faulty products. By leveraging IoT in quality control, manufacturers can ensure consistent product quality, enhance customer satisfaction, and maintain a competitive edge in the market.
Benefits of IoT in Manufacturing
Implementing IoT in manufacturing brings a multitude of benefits that have a direct impact on business performance. Let's explore some of the key advantages.
Increased Efficiency and Productivity
By leveraging IoT, manufacturers can optimize their operations, resulting in improved efficiency and productivity. Real-time data from IoT sensors allows for better decision-making and enables predictive maintenance, reducing unplanned downtime. Additionally, IoT-enabled automation systems can streamline workflows, eliminating manual processes and minimizing errors.
Improved Safety Measures
Safety is a paramount concern in manufacturing environments, with potential hazards and risks present. IoT offers enhanced safety measures by providing real-time monitoring and alerts. For instance, sensors can detect abnormal temperature levels or hazardous gases, triggering alarms or shutting down equipment. This not only protects employees but also safeguards the manufacturing facility from potential accidents.
Cost Reduction
IoT can also contribute to cost reduction in manufacturing operations. By optimizing production processes and improving efficiency, manufacturers can minimize waste and reduce energy consumption. IoT-enabled predictive maintenance allows for the timely replacement of parts, reducing the likelihood of expensive breakdowns. Additionally, IoT analytics can identify areas of improvement, helping manufacturers optimize resource allocation.
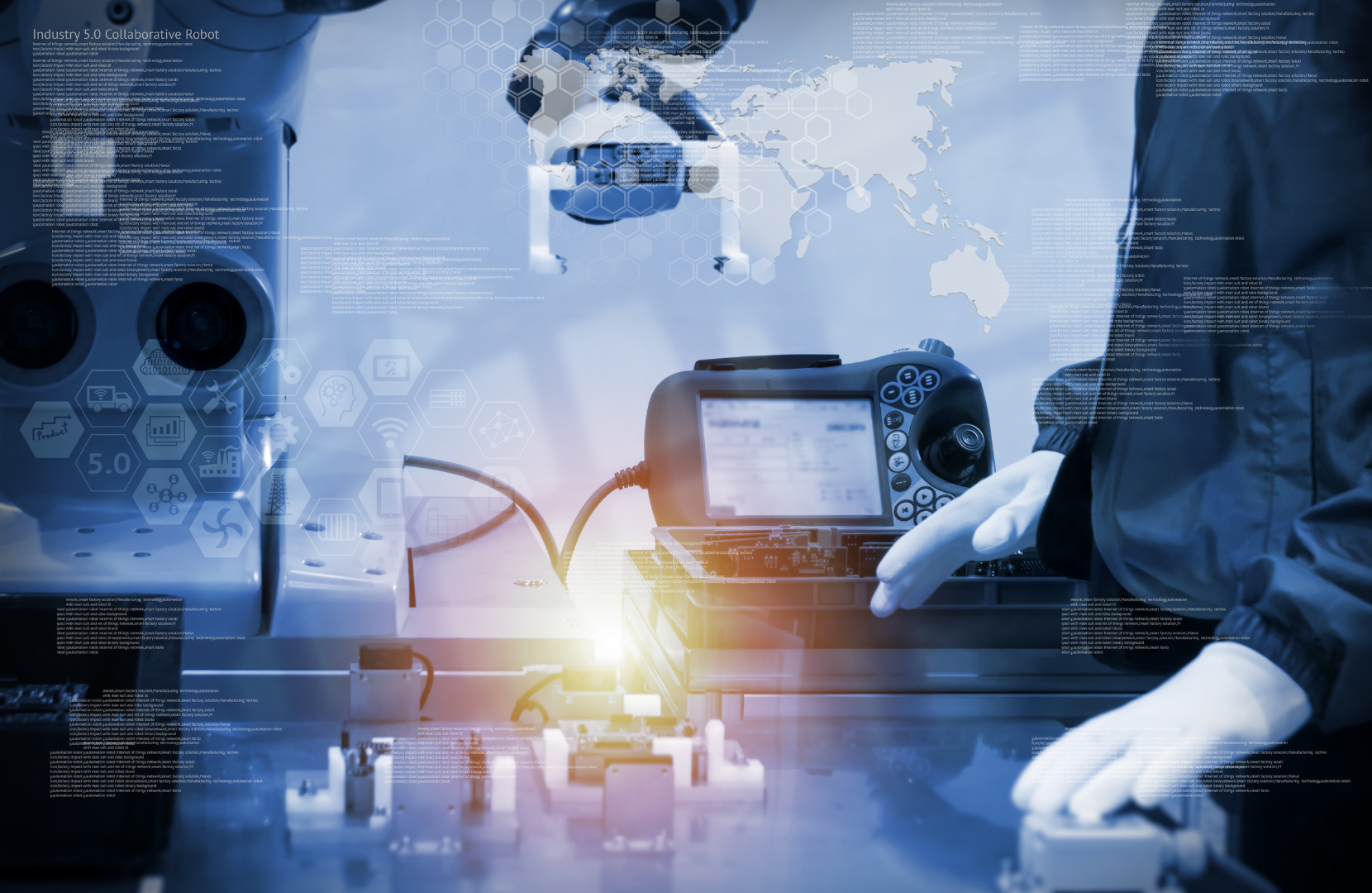
Real-world Examples of IoT in Manufacturing
While the benefits of IoT in manufacturing are evident, it is essential to understand how these advantages translate into real-world applications. Let's explore two case studies showcasing the impact of IoT in manufacturing processes.
Case Study: IoT in Automotive Manufacturing
In the automotive industry, IoT has revolutionized manufacturing processes. IoT sensors are deployed throughout the assembly line, collecting data on various parameters such as torque, temperature, and vibration. This data is analyzed in real-time, allowing for predictive maintenance and quality control. By leveraging IoT, automotive manufacturers have been able to improve production efficiency, reduce defects, and enhance overall product quality.
Case Study: IoT in Electronics Manufacturing
Electronics manufacturing heavily relies on precise assembly processes and quality control. IoT has played a significant role in this sector by enabling real-time monitoring of manufacturing equipment and ensuring compliance with strict quality standards. By integrating IoT sensors into the production line, electronics manufacturers can identify and rectify defects promptly. This leads to reduced rework, higher product reliability, and improved customer satisfaction.
Challenges and Solutions in Implementing IoT in Manufacturing
While the benefits of IoT in manufacturing are compelling, implementing IoT solutions does come with its challenges. Here are two key challenges and proposed solutions to help overcome them.
Security Concerns
As more devices are connected to the internet, the risk of cybersecurity threats increases. In manufacturing, compromised IoT devices can lead to data breaches, production disruptions, and even physical harm. It is crucial for manufacturers to prioritize security measures by implementing robust encryption protocols, regular software updates, and network segmentation. Additionally, training employees on IoT security best practices can help mitigate risks.
Integration with Existing Systems
Integrating IoT solutions with existing manufacturing systems can be complex, as it requires compatibility and interoperability between different technologies. To address this challenge, manufacturers should carefully plan the implementation process and collaborate with experienced IoT solution providers. Conducting thorough testing and ensuring seamless integration with existing systems are vital for a successful deployment.
Conclusion
The integration of IoT in manufacturing has the potential to revolutionize the industry. By leveraging IoT-enabled devices and the wealth of data they generate, manufacturers can improve efficiency, enhance quality control, and reduce costs. Real-world examples like automotive and electronics manufacturing illustrate the impact of IoT on different sectors. Despite challenges such as security concerns and system integration, the benefits outweigh the potential drawbacks. As manufacturing continues to embrace IoT, the future of production looks promising, with increased automation, optimized processes, and improved overall performance.