Imagine a world where you can effortlessly design and create your own clothes from the comfort of your own home. This may sound like something out of a science fiction movie, but with the advent of 3D printing technology, it is quickly becoming a reality. 3D printing has taken the fashion industry by storm, revolutionizing the way we design, produce, and consume clothing. In this article, we will explore how 3D printing technology is reshaping the fashion industry, from its basic principles to its future potential.
Understanding 3D Printing Technology
Before diving into the impact of 3D printing on the fashion industry, it is important to understand the basics of this groundbreaking technology. 3D printing, also known as additive manufacturing, is a process that constructs three-dimensional objects by layering materials on top of each other. The process starts with a computer-aided design (CAD) file, which provides a blueprint for the desired object. This file is then sent to a 3D printer, which uses various materials, such as plastics, metals, or even fabrics, to build the object layer by layer.
The Basics of 3D Printing
The first step in the 3D printing process is creating a digital model of the object you want to print. This can be done using specialized software or by scanning an existing object using a 3D scanner. Once the digital model is ready, it is sliced into thin layers, which the 3D printer will then build up one by one. The printer does this by depositing or curing the material in the desired shape, layer by layer, until the object is fully formed. This layer-by-layer approach allows for incredible design freedom and intricate detailing that was previously impossible to achieve with traditional manufacturing methods.
Imagine you want to create a custom-designed piece of jewelry. With 3D printing, you can easily bring your vision to life. You start by sketching your design on paper, and then use CAD software to translate it into a digital model. Once the digital model is ready, you can make adjustments and refine the design until it is perfect. This level of precision and flexibility is what sets 3D printing apart from traditional manufacturing methods.
Once the design is finalized, the 3D printer takes over. It reads the digital model and starts building the object layer by layer. If you were to watch the printer in action, you would see it depositing tiny droplets of material, carefully following the instructions from the CAD file. Layer by layer, the object takes shape, until finally, you have a physical representation of your original design.
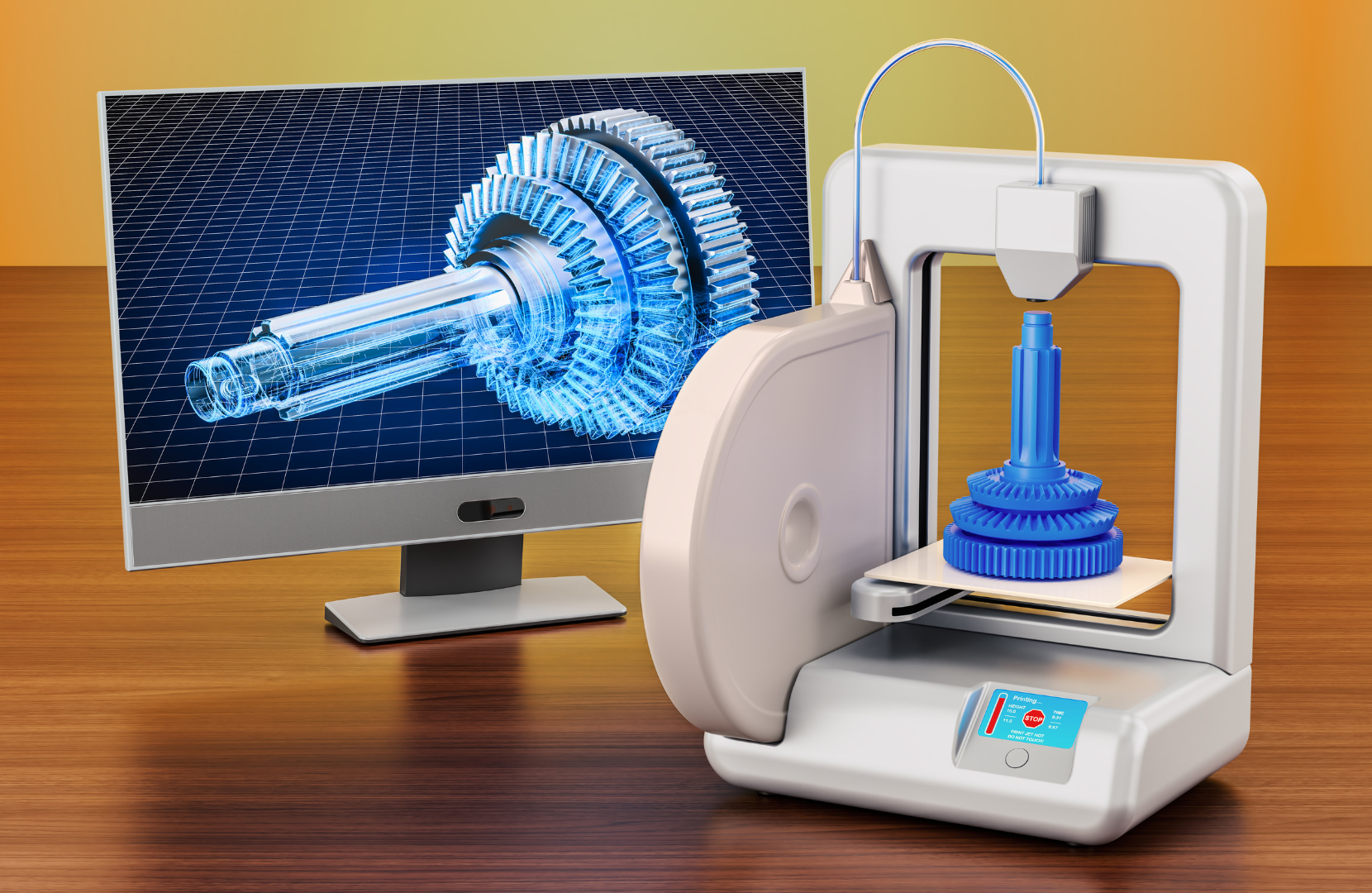
Different Types of 3D Printing Techniques
There are several different types of 3D printing techniques, each with its own strengths and limitations. Some of the most commonly used techniques in the fashion industry include:
- Fused Deposition Modeling (FDM): This technique involves extruding a continuous stream of molten material through a nozzle to build up the layers of the object.
- Stereolithography (SLA): SLA uses a liquid resin that is solidified layer by layer using a laser or UV light.
- Selective Laser Sintering (SLS): SLS uses a laser to selectively fuse powdered material together to form the object.
These are just a few examples of the many 3D printing techniques available today, each with its own unique advantages and applications in the world of fashion.
For example, Fused Deposition Modeling (FDM) is often used in the production of wearable accessories. Its ability to use a wide range of materials, including flexible filaments, makes it ideal for creating intricate designs that can be worn comfortably. On the other hand, Stereolithography (SLA) is commonly used for creating high-detail prototypes and small-scale production runs. Its ability to produce smooth surfaces and fine details makes it a popular choice for creating jewelry and other fashion accessories.
Selective Laser Sintering (SLS), on the other hand, is often used for creating functional parts and components. It can work with a wide range of materials, including nylon and metal powders, allowing for the production of durable and lightweight objects. This technique is particularly useful in the creation of custom shoe soles, eyewear frames, and even clothing with integrated functional elements.
As technology continues to advance, new 3D printing techniques are being developed, pushing the boundaries of what is possible in the world of fashion. From bio-printing living materials to using recycled plastics, the future of 3D printing holds immense potential for revolutionizing the way we design, create, and wear fashion.

The Intersection of 3D Printing and Fashion
Now that we have a basic understanding of 3D printing technology, let's explore how it intersects with the world of fashion. The fashion industry is known for its constant need for innovation and creativity, and 3D printing provides a new platform for designers to push the boundaries of what is possible.
Early Adopters in the Fashion Industry
While 3D printing is still relatively new in the fashion industry, there are already a number of designers and brands who have embraced this technology. These early adopters have utilized 3D printing to create avant-garde designs, unique accessories, and even entire garments. By experimenting with new materials and pushing the limits of traditional design, these pioneers are reshaping the future of fashion.
Case Studies of 3D Printed Fashion
One way to understand the impact of 3D printing on the fashion industry is by looking at some fascinating case studies. For example, Dutch fashion designer Iris van Herpen has gained international acclaim for her intricate 3D printed garments, which blur the line between fashion and art. Her designs showcase the endless possibilities of 3D printing, from intricate lace-like patterns to fluid and organic shapes.
Another noteworthy case study is the collaboration between fashion designer Julia Koerner and sportswear giant Adidas. Together, they created the "Futurecraft 4D" shoe, which features a 3D printed midsole that is not only lightweight and durable but also tailored to each individual's foot shape. This customization and personalized fit are only possible through 3D printing technology.
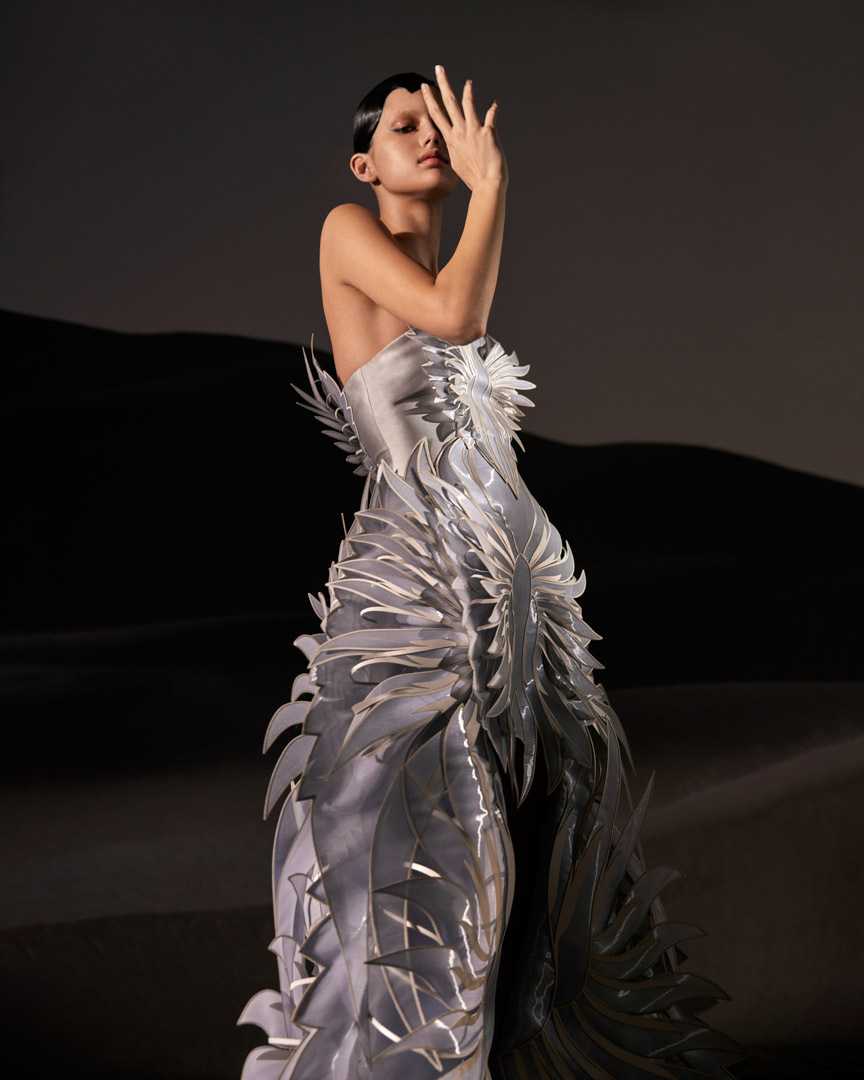
Benefits of 3D Printing in Fashion
Now that we have explored the intersection of 3D printing and fashion, let's delve into the numerous benefits that this technology offers to the industry.
Speed and Efficiency
One of the key advantages of 3D printing in fashion is its ability to significantly speed up the design and production process. Traditional manufacturing methods can be slow and time-consuming, involving multiple prototypes and iterations. With 3D printing, designers can quickly turn their ideas into physical objects, reducing the time from concept to creation. This speed and efficiency allow for faster product development cycles and shorter lead times.
Customization and Personalization
Another major advantage of 3D printing in fashion is the ability to create customized and personalized items. Each person has a unique body shape and size, and traditional mass production often fails to cater to individual needs. 3D printing allows designers to create garments and accessories that are tailored to each individual's measurements, ensuring a perfect fit. This customization not only enhances the consumer's experience but also reduces waste by eliminating the need for excess inventory.
Sustainability and Waste Reduction
The fashion industry has long been criticized for its negative impact on the environment, with fast fashion and excessive waste being major concerns. 3D printing offers a more sustainable alternative by significantly reducing material waste. Unlike traditional manufacturing methods, which often involve cutting and discarding excess fabric, 3D printing only uses the amount of material necessary to create the desired object. This reduction in waste can have a significant positive impact on the environment and help the fashion industry move towards a more sustainable future.
Challenges and Limitations of 3D Printing in Fashion
While the potential of 3D printing in fashion is immense, there are still several challenges and limitations that need to be overcome for widespread adoption.
Material Limitations
One of the main challenges in 3D printing fashion is the limited range of materials available. While there have been advancements in printing with fabrics and other flexible materials, the majority of 3D printed fashion is still made using rigid plastics. This limits the variety of textures, colors, and finishes that can be achieved with 3D printed garments and accessories. However, ongoing research and development in this field are continuously expanding the material options available for 3D printing in fashion.
Cost and Accessibility
Another limitation of 3D printing in fashion is the high cost of the technology and the limited accessibility for designers and consumers. 3D printers, especially those capable of printing complex and detailed objects, can be quite expensive. Additionally, the expertise required to operate and maintain these printers can be a barrier for many designers. However, as the technology advances and becomes more widespread, the cost and accessibility of 3D printing in fashion are expected to improve.
The Future of 3D Printing in Fashion
As 3D printing continues to evolve and gain traction in the fashion industry, it is exciting to imagine what the future holds.
Emerging Trends and Innovations
One of the emerging trends in 3D printing is the use of sustainable and biodegradable materials. Designers and researchers are exploring alternative materials, such as algae-based filaments and recycled plastics, to create more eco-friendly 3D printed fashion. This focus on sustainability aligns with the growing demand for ethical and environmentally conscious fashion.
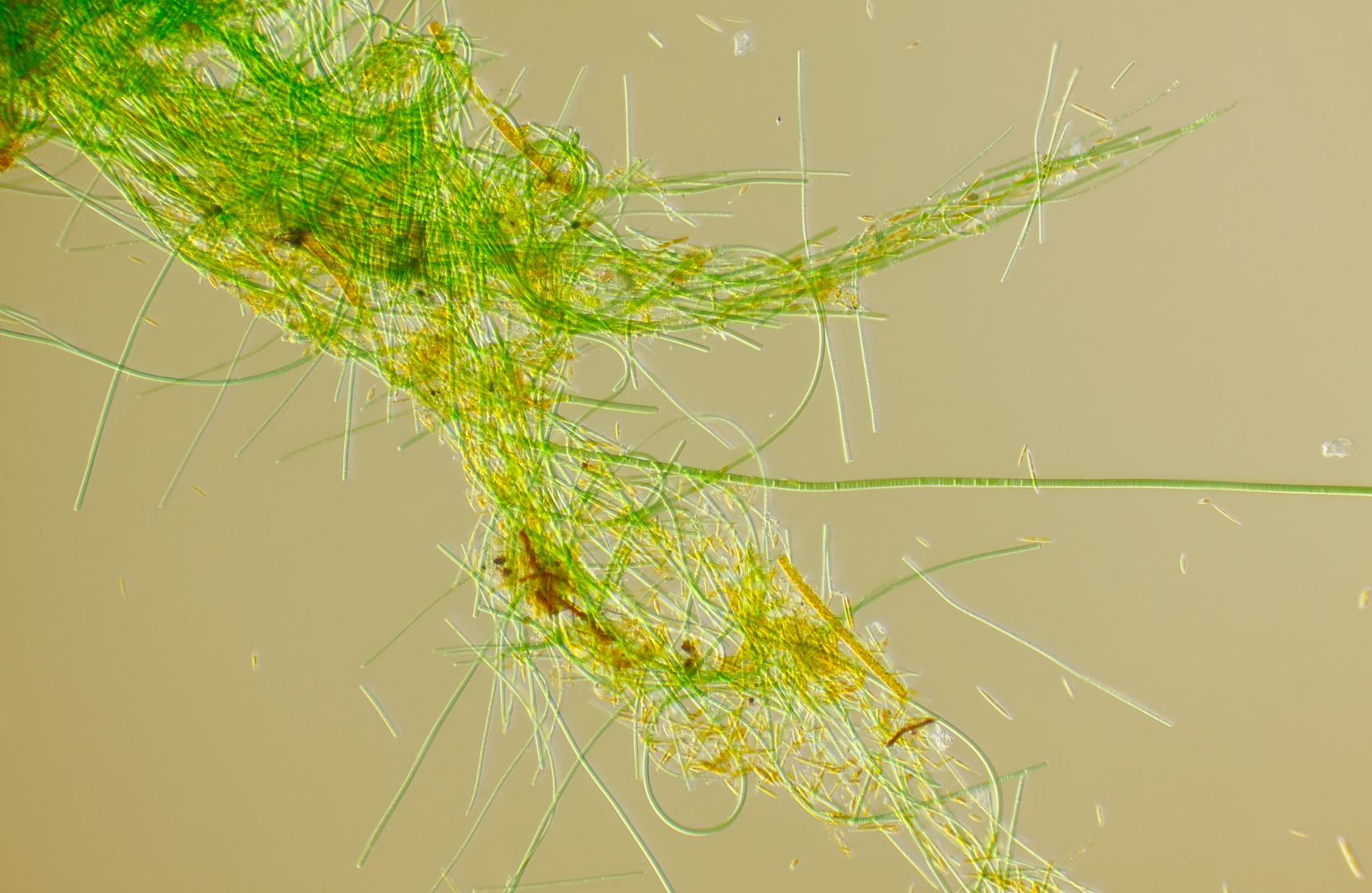
Predictions for the Future of Fashion Technology
Looking ahead, experts predict that 3D printing will play an increasingly important role in the future of fashion technology. From on-demand production to personalized designs, 3D printing has the potential to transform the entire fashion supply chain. As the technology becomes more accessible and the market demand for customization continues to grow, 3D printed fashion is poised to redefine the industry as we know it.
Conclusion
3D printing is revolutionizing the fashion industry, opening up new possibilities for design, production, and customization. As this technology continues to evolve, we can expect to see its impact on the industry expand, leading to a more sustainable, innovative, and personalized future for fashion.