La impresión 3D está revolucionando la forma de diseñar y fabricar productos. Una de las técnicas más innovadoras y versátiles en este campo es el sinterizado selectivo por láser (SLS). Al aprovechar la potencia de los láseres y los materiales en polvo, el SLS se ha convertido en un revulsivo en el sector de la impresión 3D.
Conceptos básicos de la impresión 3D
Antes de profundizar en los entresijos de la SLS, es fundamental comprender los fundamentos de la impresión 3D. Esta revolucionaria tecnologÃa permite crear objetos capa a capa, a partir de modelos digitales. A diferencia de los métodos de fabricación tradicionales, que implican procesos sustractivos como el taladrado o el corte, la impresión 3D es un proceso aditivo, en el que los materiales se acumulan para formar el producto final.
A lo largo de los años, la impresión 3D ha experimentado una notable evolución, desde sus humildes comienzos como herramienta de creación de prototipos hasta convertirse en una tecnologÃa capaz de fabricar estructuras complejas con notable precisión.
La evolución de la impresión 3D
Cuando apareció la impresión 3D en la década de 1980, se utilizaba principalmente para la creación rápida de prototipos. Los diseñadores e ingenieros podÃan transformar rápidamente sus ideas en prototipos fÃsicos, lo que permitÃa una iteración y un desarrollo del producto más rápidos. Esta innovación revolucionó la industria manufacturera, permitiendo a las empresas ahorrar tiempo y recursos en el proceso de desarrollo de productos.
A medida que la tecnologÃa avanzaba, encontró aplicaciones en diversas industrias, como la aeroespacial, la automovilÃstica y la sanitaria. En el sector aeroespacial, la impresión 3D se ha utilizado para crear componentes ligeros pero resistentes para aeronaves, reduciendo el consumo de combustible y mejorando el rendimiento general. En la industria del automóvil, la impresión 3D ha permitido la producción de piezas y prototipos personalizados, acelerando la fase de diseño y pruebas. En la sanidad, la impresión 3D ha abierto nuevas posibilidades en la medicina personalizada, permitiendo la creación de implantes y prótesis especÃficos para cada paciente.
Hoy en dÃa, las impresoras 3D son más accesibles y asequibles, lo que ha allanado el camino para su adopción generalizada y la innovación. Desde pequeñas impresoras de sobremesa hasta grandes máquinas industriales, las empresas y los particulares pueden aprovechar ahora el poder de la impresión 3D para crear productos personalizados. Esta democratización de la fabricación ha permitido a emprendedores y creadores dar vida a sus ideas, fomentando una cultura de innovación y creatividad.
Componentes clave de una impresora 3D
Una impresora 3D se compone de varios componentes cruciales que trabajan juntos para transformar diseños digitales en objetos fÃsicos. Comprender estos componentes es esencial para cualquiera que desee explorar el mundo de la impresión 3D:
- La plataforma de construcción: Es la plataforma sobre la que se construye el objeto capa a capa. Proporciona una base estable para el proceso de impresión y garantiza la precisión de cada capa.
- Cabezal de impresión o extrusor: El cabezal de impresión deposita o extrude el material, siguiendo las especificaciones del diseño digital. Calienta el material hasta su punto de fusión y controla con precisión su flujo, lo que permite crear formas y estructuras intrincadas.
- Sistema de control: El sistema de control coordina los movimientos y las operaciones de la impresora para garantizar la deposición precisa de los materiales. Interpreta el archivo de diseño digital y lo traduce en instrucciones especÃficas para los motores y el extrusor de la impresora.
- Fuente de alimentación: La fuente de alimentación suministra la energÃa necesaria para accionar los componentes de la impresora, como los motores y los elementos calefactores. Garantiza un suministro de energÃa estable y constante, lo que permite imprimir sin interrupciones.
- Filamento o resina: El material utilizado para la impresión 3D, ya sea filamento o resina, desempeña un papel crucial a la hora de determinar las propiedades finales del objeto impreso. Los distintos materiales ofrecen diferentes niveles de resistencia, flexibilidad y durabilidad, lo que permite una amplia gama de aplicaciones.
- Software: El software utilizado en la impresión 3D se encarga de crear y editar los diseños digitales, asà como de prepararlos para la impresión. Permite a los usuarios manipular y personalizar sus diseños, ajustando parámetros como el tamaño, la orientación y la densidad de relleno.
Al comprender estos componentes clave, las personas pueden apreciar mejor los entresijos de la impresión 3D y explorar las posibilidades ilimitadas que ofrece en términos de diseño, fabricación e innovación.
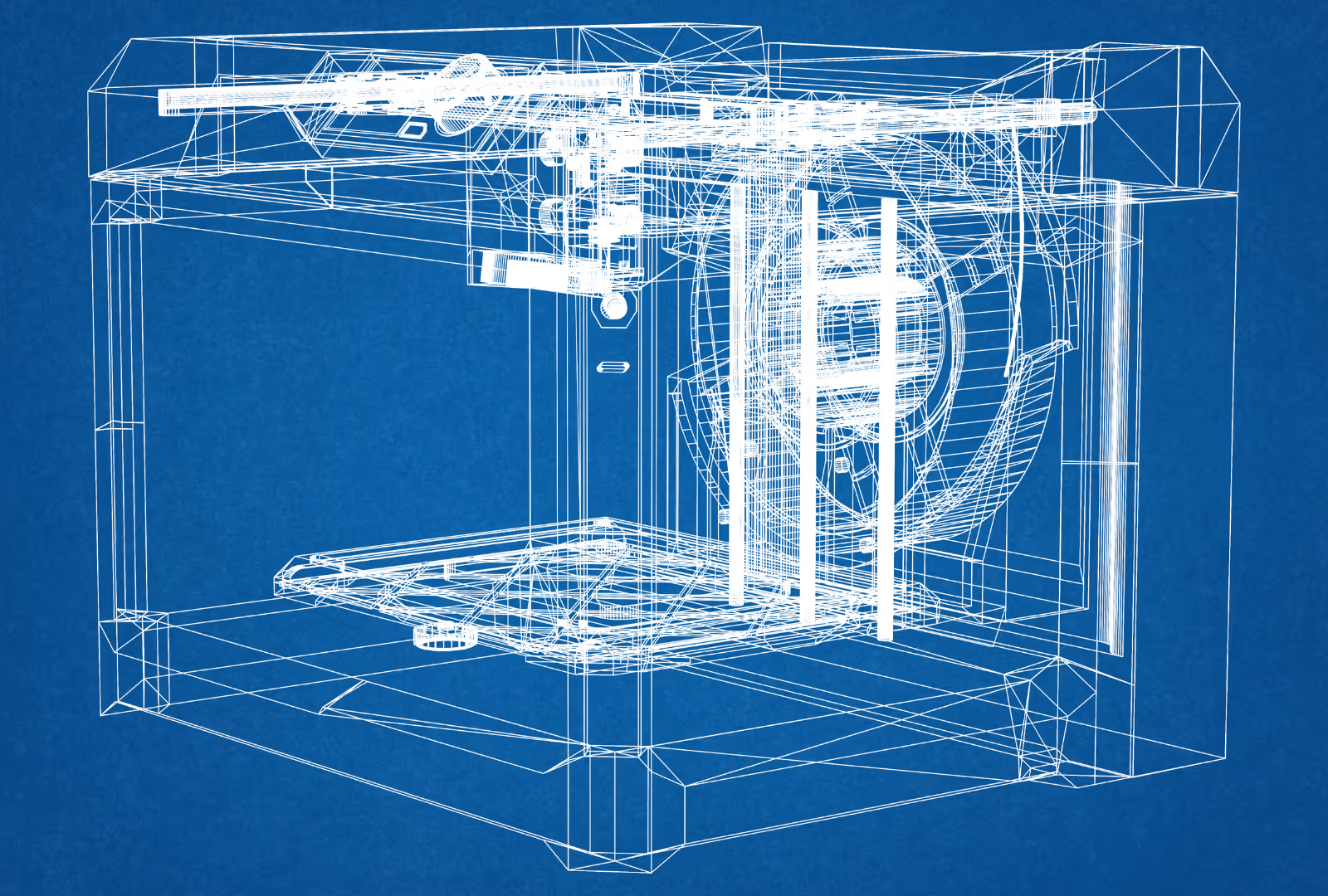
Introducción al sinterizado selectivo por láser (SLS)
Ahora que hemos sentado las bases de la impresión 3D, vamos a adentrarnos en los detalles del Sinterizado Láser Selectivo. SLS es una técnica de impresión 3D de fusión de lecho de polvo que utiliza láseres para fusionar selectivamente materiales en polvo, capa por capa, para crear objetos complejos.
Comparado con otros métodos de impresión 3D, como el modelado por deposición fundida (FDM) o la estereolitografÃa (SLA), el SLS ofrece claras ventajas en cuanto a versatilidad y capacidad de materiales.
¿Cómo funciona el SLS?
El SLS comienza con una fina capa de material en polvo esparcida por la plataforma de construcción. A continuación, un láser de alta potencia funde o sinteriza selectivamente las partÃculas de polvo, formando la forma deseada. A continuación, la plataforma de construcción desciende y se extiende una nueva capa de polvo, repitiéndose el proceso hasta que se fabrica todo el objeto.
El uso de láseres en SLS permite un control preciso del proceso de fusión, lo que da como resultado impresiones muy precisas y detalladas. Además, la capacidad de imprimir estructuras autoportantes elimina la necesidad de materiales de soporte, lo que hace que el SLS sea ideal para diseños intrincados.
Veamos el proceso más de cerca. Cuando el láser explora el material en polvo, crea calor localizado, lo que hace que las partÃculas se fusionen. La intensidad y la duración del láser se controlan cuidadosamente para garantizar que se aplica la cantidad correcta de calor, lo que da como resultado una unión fuerte. A medida que la plataforma de construcción desciende, un rodillo o una cuchilla extiende una nueva capa de polvo por encima, lista para la siguiente ronda de escaneado láser. Este enfoque por capas permite crear geometrÃas complejas y detalles intrincados que serÃan difÃciles de conseguir con los métodos de fabricación tradicionales.
Otra ventaja del SLS es su capacidad para producir objetos con buenas propiedades mecánicas. La fusión de las partÃculas en polvo crea una estructura sólida y densa que da lugar a piezas resistentes y duraderas. Esto hace que el SLS sea adecuado para una amplia gama de aplicaciones, como prototipos funcionales, piezas de uso final e incluso implantes médicos.
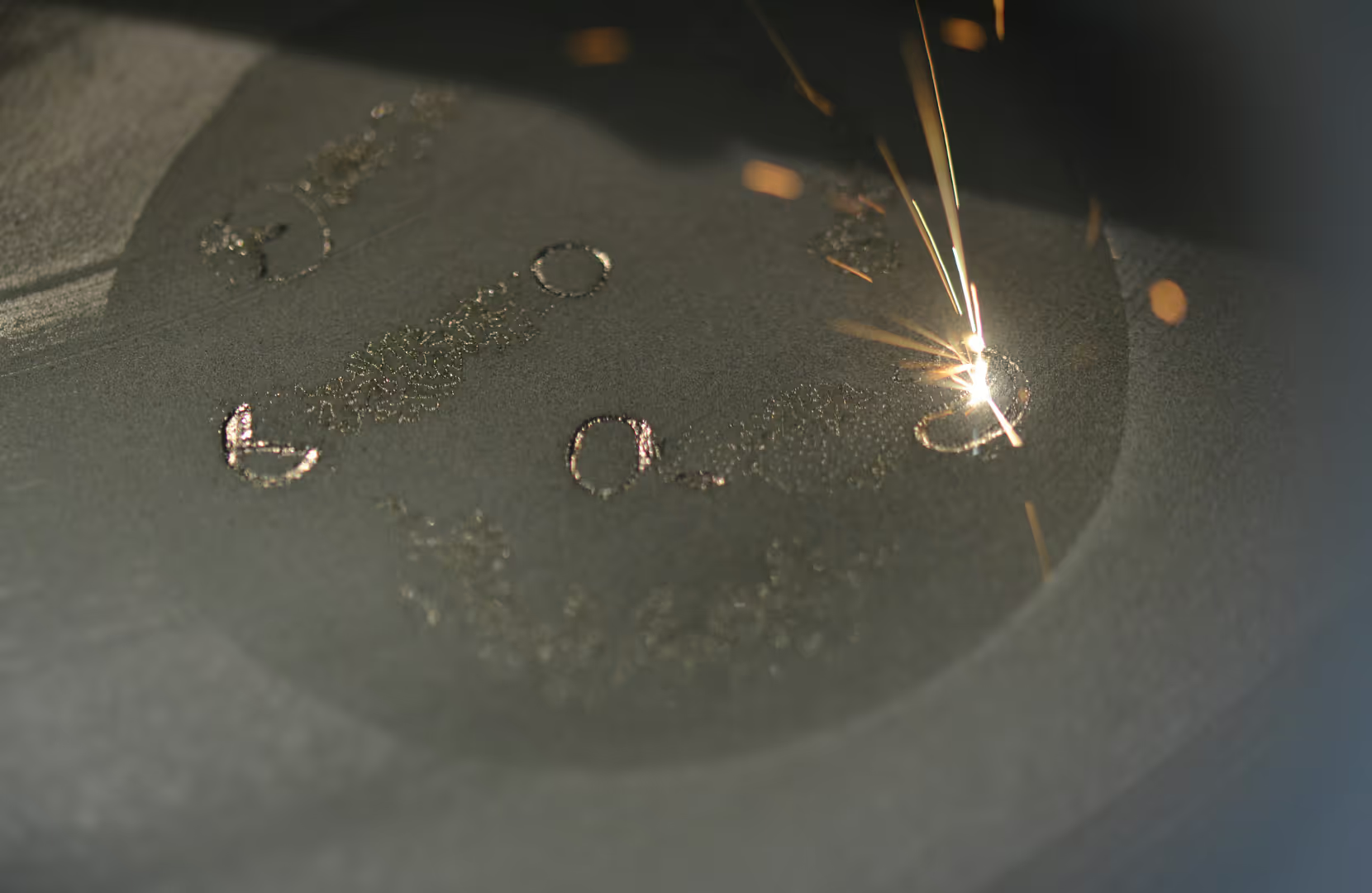
Materiales utilizados en SLS
Una de las ventajas significativas del SLS es su amplia gama de materiales compatibles. A diferencia de otras técnicas de impresión 3D que se limitan a materiales especÃficos, el SLS puede trabajar con una gran variedad de polvos, incluidos plásticos, metales y cerámicas.
Entre los plásticos más utilizados en SLS se encuentran el nailon, el policarbonato y el polipropileno. Estos materiales ofrecen excelentes propiedades mecánicas, lo que los hace adecuados para prototipos funcionales y piezas de uso final. El nailon, en particular, se utiliza mucho en SLS por su resistencia, flexibilidad y resistencia al calor.
Los polvos metálicos, como el aluminio, el titanio y el acero, también pueden utilizarse en SLS, lo que permite fabricar componentes metálicos con geometrÃas complejas. Esto abre nuevas posibilidades en sectores como el aeroespacial, la automoción y la sanidad, donde hay una gran demanda de piezas metálicas ligeras pero resistentes.
Además de plásticos y metales, el SLS también puede trabajar con polvos cerámicos. La cerámica ofrece propiedades únicas, como resistencia a altas temperaturas, aislamiento eléctrico y biocompatibilidad, lo que la hace adecuada para una amplia gama de aplicaciones, como la electrónica, la industria aeroespacial y los dispositivos médicos.
Cabe señalar que la elección del material para SLS depende de los requisitos especÃficos de la aplicación. Factores como las propiedades mecánicas, la estabilidad térmica, la resistencia quÃmica y el coste desempeñan un papel crucial en la selección del material.
Comparación de SLS con otras técnicas de impresión 3D
Aunque el SLS comparte similitudes con otras técnicas de impresión 3D, se distingue por sus capacidades y aplicaciones. Veamos con más detalle cómo se compara el SLS con el modelado por deposición fundida (FDM) y la estereolitografÃa (SLA).
SLS frente al modelado por deposición fundida (FDM)
La FDM, una de las técnicas de impresión 3D más utilizadas, consiste en extrudir filamentos termoplásticos fundidos para construir objetos capa a capa. Aunque la FDM es rentable y accesible, está limitada en cuanto a acabado superficial y compatibilidad de materiales. SLS, en cambio, ofrece una mejor calidad de superficie y versatilidad de materiales, lo que la hace adecuada para una gama más amplia de aplicaciones.
SLS frente a la estereolitografÃa (SLA)
La SLA se basa en la fotopolimerización para crear objetos mediante el curado selectivo de resina lÃquida con un láser UV. La SLA produce impresiones de alta resolución con superficies lisas, pero está limitada por la necesidad de estructuras de soporte y la disponibilidad de resinas compatibles. El SLS, con su capacidad para imprimir estructuras autoportantes y trabajar con una mayor variedad de materiales, supera estas limitaciones.
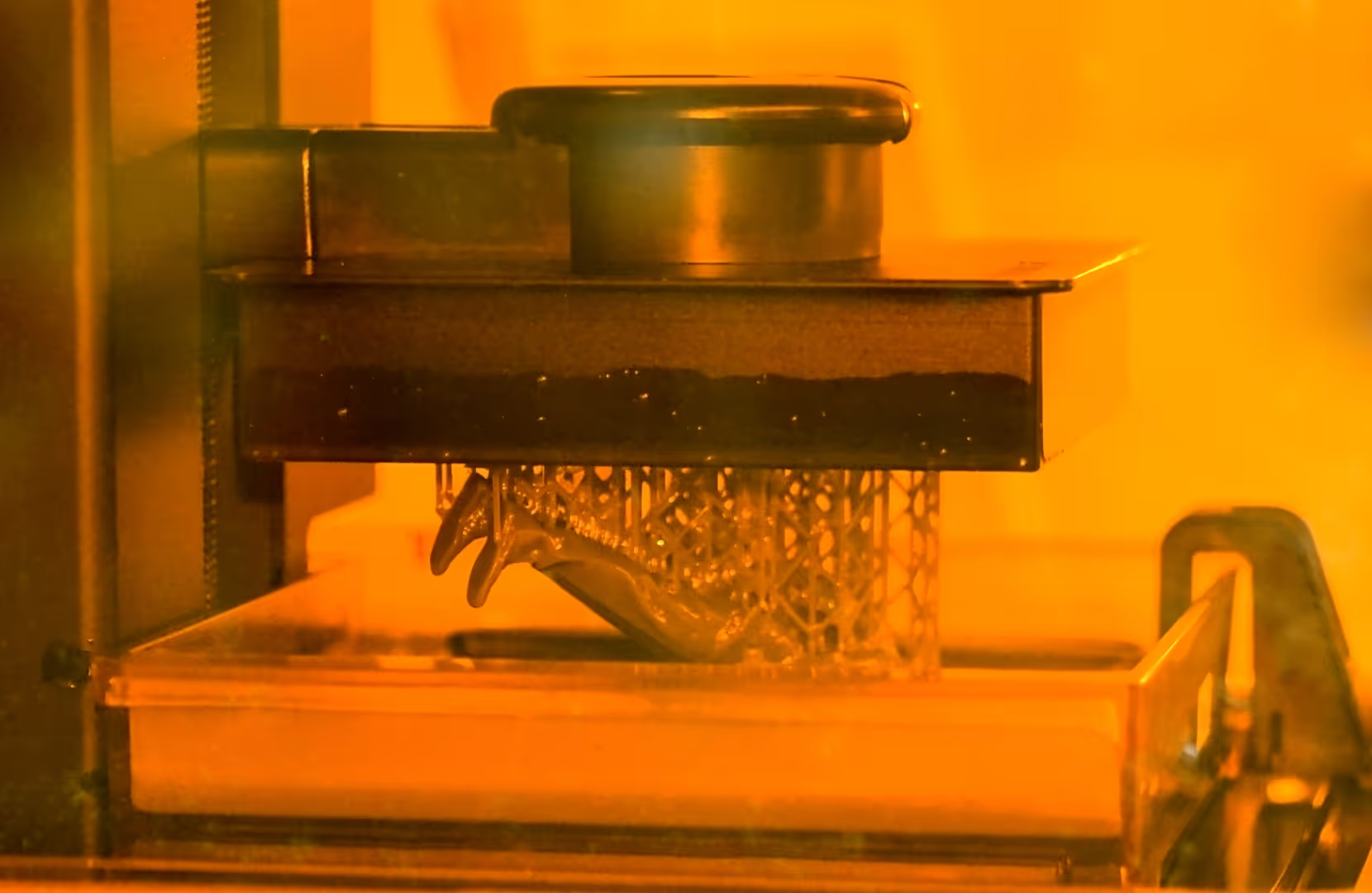
Ventajas del sinterizado selectivo por láser
Ahora que ya conocemos el funcionamiento interno del SLS y su comparación con otras técnicas de impresión 3D, vamos a explorar sus ventajas únicas, que lo convierten en un cambio radical.
Detalle y precisión superiores
El SLS ofrece un nivel excepcional de detalle y precisión gracias a los láseres de alta potencia utilizados en el proceso. Los láseres pueden alcanzar resoluciones de hasta 25 micras, lo que se traduce en impresiones precisas y complejas. Este nivel de precisión hace que el SLS sea adecuado para aplicaciones que exigen tolerancias estrechas y caracterÃsticas complejas.
Mayor versatilidad de materiales
A diferencia de otras técnicas de impresión 3D, el SLS no está limitado a una gama especÃfica de materiales. Con SLS es posible trabajar con diversos materiales en polvo, lo que permite crear prototipos funcionales, piezas de uso final e incluso productos a medida. Esta versatilidad permite a empresas y diseñadores explorar distintos materiales y optimizar sus diseños para fines especÃficos.
Aplicaciones del SLS en diversas industrias
Gracias a sus ventajas únicas, el SLS tiene aplicaciones en diversos sectores, ofrece soluciones innovadoras y amplÃa los lÃmites de los procesos de fabricación tradicionales. Exploremos algunas áreas clave en las que el SLS está teniendo un impacto significativo.
SLS en el ámbito médico
El SLS ha revolucionado el campo de la medicina al permitir la producción de prótesis, órtesis e implantes personalizados. La capacidad de imprimir geometrÃas complejas e incorporar diseños especÃficos para cada paciente ha transformado la forma de crear dispositivos médicos. La SLS también facilita la creación rápida de prototipos de herramientas quirúrgicas y modelos anatómicos, lo que permite mejorar la planificación y la formación quirúrgicas.
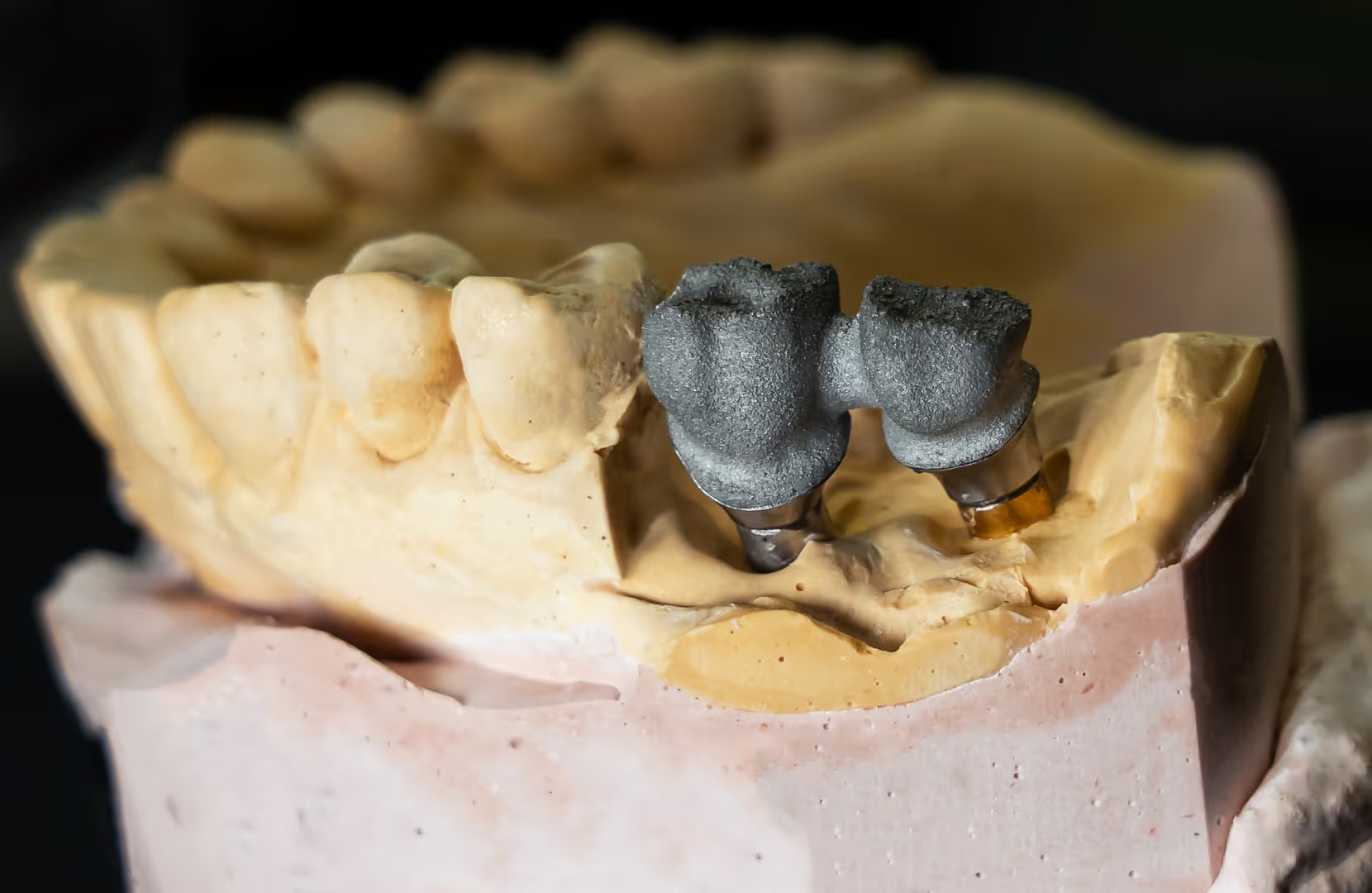
SLS en la fabricación de automóviles
La industria del automóvil ha adoptado el SLS por su capacidad para producir componentes ligeros con diseños intrincados. El SLS permite crear conductos de aire complejos, canales de refrigeración conformados y prototipos funcionales que pueden soportar procesos de prueba y validación. Con el SLS, los fabricantes pueden reducir los costes de utillaje, mejorar el rendimiento de los productos y acelerar sus ciclos de desarrollo.
Conclusión
El sinterizado selectivo por láser (SLS) ha cambiado las reglas del juego del sector de la impresión 3D. Al aprovechar el láser y los materiales en polvo, el SLS ofrece un nivel superior de detalle, precisión y versatilidad de materiales. Con aplicaciones en diversos sectores, el SLS sigue ampliando los lÃmites de los procesos de fabricación tradicionales. A medida que avanza la tecnologÃa y evolucionan los materiales, el SLS está preparado para dar forma al futuro de la fabricación, allanando el camino para productos innovadores y personalizados.